<< View SCS Blog
Conformal Coatings Enhance Coil Winding Designs
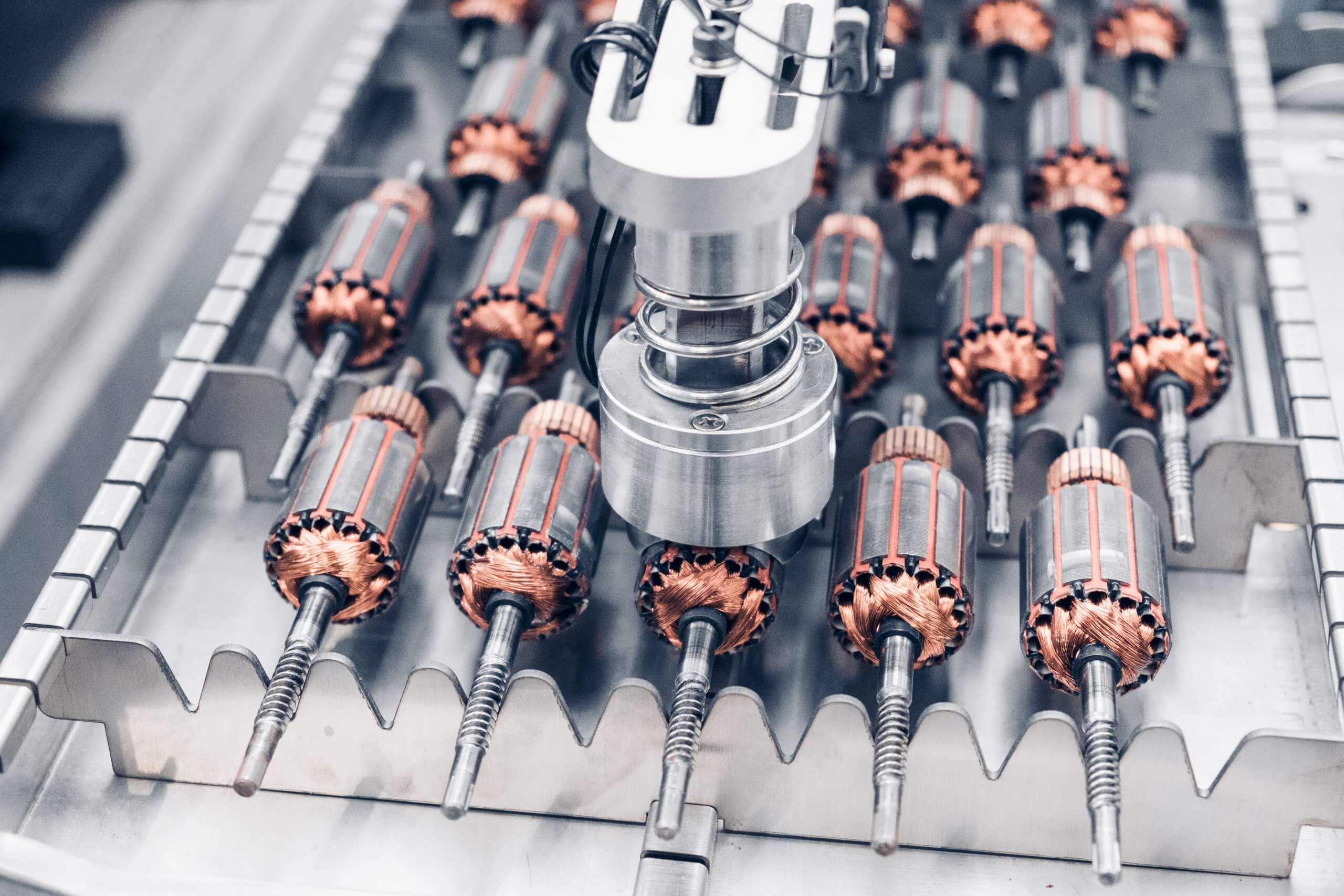
With the evolution of e-mobility, medical electronics and electric motors, the demand for advanced coil winding designs is growing. The manufacture of these windings can be broken down into three distinct phases: pre-winding, winding and post-winding. Each phase presents different challenges that can impact the robustness and longevity of the application’s design. To protect and enhance their overall coil-winding designs, manufacturers regularly turn to conformal coatings.
During pre-winding in rotor shaft manufacturing, for example, components need to be kept electrically isolated from the core and/or any winding that is to be installed during the subsequent winding phase. This process can be complicated by the rotor shaft’s constant exposure to oils and other fluids. A thin, lightweight conformal coating, like Parylene, adds little dimension or mass while also providing necessary corrosion resistance and electrical isolation. Parylenes are commonly used for coating small- to medium-sized rotor shafts while liquid conformal coatings like acrylic or silicones are often used for larger-sized shafts.
The objective of the winding phase is to get the tightest winding possible while keeping the wires from breaking and ensuring the electrical insulation between the core and wire winding stays intact. Wire breakage can cause production issues, and decreased performance of the rotor shaft can occur with ineffective insulation resistance. Less than optimal performance can be the final result when the tightest winding is not achieved. Ultra-thin Parylene has been proven to strengthen the wires enabling the tightest winding possible.
Finally, in the post-winding phase, the rotor shaft’s design is complete and ready for installation into applications such as powered electrosurgical tools, electric vehicle motors and aircraft engines, to name a few. Depending on the coil winding’s designated environment, a conformal coating can be used to protect it from moisture and corrosion and to provide electrical isolation. Parylene and/or liquid conformal coatings are commonly used to increase the rotor shaft’s reliability and prevent failure while in use.
Coil windings are an important technology used in a myriad of applications. Existing and new challenges for optimal functionality will arise, and conformal coatings are a key design solution to help enhance the robustness of the winding.
If you would like more information about SCS conformal coating services in the use of coil windings, contact SCS online or call +1.317.244.1200.
Global Coverage Issue 97, Fall 2024