Conformal Coatings Overview
Conformal Coating Removal for Board and Component Repair
Because manufacturers are often faced with the task of repairing components on circuit boards, it is important to consider how the choice of a particular coating material may affect the ability to rework and repair assemblies. The need for rework or repair of a conformal coating can arise at any time after completion of an assembly due to a variety of process or product requirements or component replacement issues. Hence, rework of conformal coatings should be addressed up front when choosing a coating chemistry.
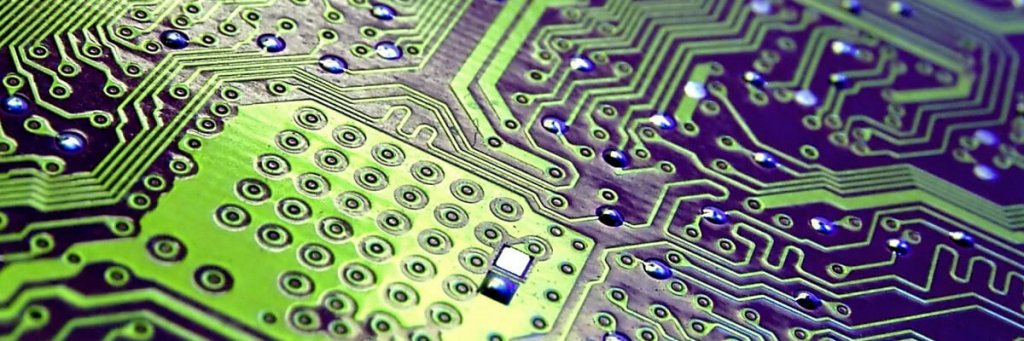
Removal of Liquid Coatings
Thermal
One removal method involves the use of heat (a solder iron, for example) in order to melt the coating for removal. Unfortunately, many coatings will not melt without long exposures to very high temperatures. These conditions can cause discoloration and leave residues as well as adversely affect solder joints and other materials or components used in the fabrication of assemblies.
Using heat in the coating removal process must be monitored to ensure that excessive temperatures do not cause delamination, lift pads or overheat surrounding temperature-sensitive devices. Extreme caution must be taken when burning conformal coatings that may emit hazardous and/or toxic vapors.
Chemical
Chemical methods are often chosen for the removal of conformal coatings. As long as the solvents used do not adversely affect the printed wiring board (PWB) or components and there are no associated environmental issues with the chosen solvent, this technique works well. There is no one-size-fits-all solvent to use across conformal coatings or applications; in fact, there are some coatings that are not removable by solvents at all due to their high resistance to chemicals.
Removal of Parylene Coatings
Parylene coatings tend to be more challenging to remove for board rework due to their insolubility to chemicals. There are a couple of documented removal methods, however, so coating removal and rework of Parylene-coated components is possible.
Thermal Removal
Laser ablation removes material from the surface by irradiating it with a laser beam. The beam can drill, cut or mark delicate materials with great precision and repeatability. Laser ablation removes very precise areas, including on high-density, difficult-to-mask parts. Applications such as microelectronics, electrosurgical devices and implantable electrodes that require very small, precise and intricate shapes to be free of coating would be well-suited for this approach. Laser ablation is less likely a viable option for the purpose of general rework as it can be cost restrictive.
Mechanical Removal
The most common method to remove Parylene coatings is by micro-abrasion. This is the fastest, most economic and ecologically-safe method for both spot and whole board Parylene coating removal. Various media, including glass beads, plastic beads, sodium bicarbonate and wheat starch, have been tested and used. To remove the coating, abrasive media can be directed at the board using pressurized air via a variety of hand-held or tabletop systems.
For more information on various methods of coating removal and the services offered by SCS, contact us today.
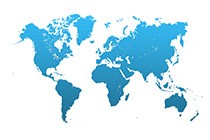
A global network of coating centers ready for your application.
Specialty Coating Systems offers customers regionally-located coating facilities to handle their engineering and production requirements. To discuss the benefits and properties of Parylene conformal coatings and your protection needs with an applications specialist, contact us online or call +1.317.244.1200.