<< View SCS Blog
SCS PrecisionCoat VI Material Applications: Underfill and Potting
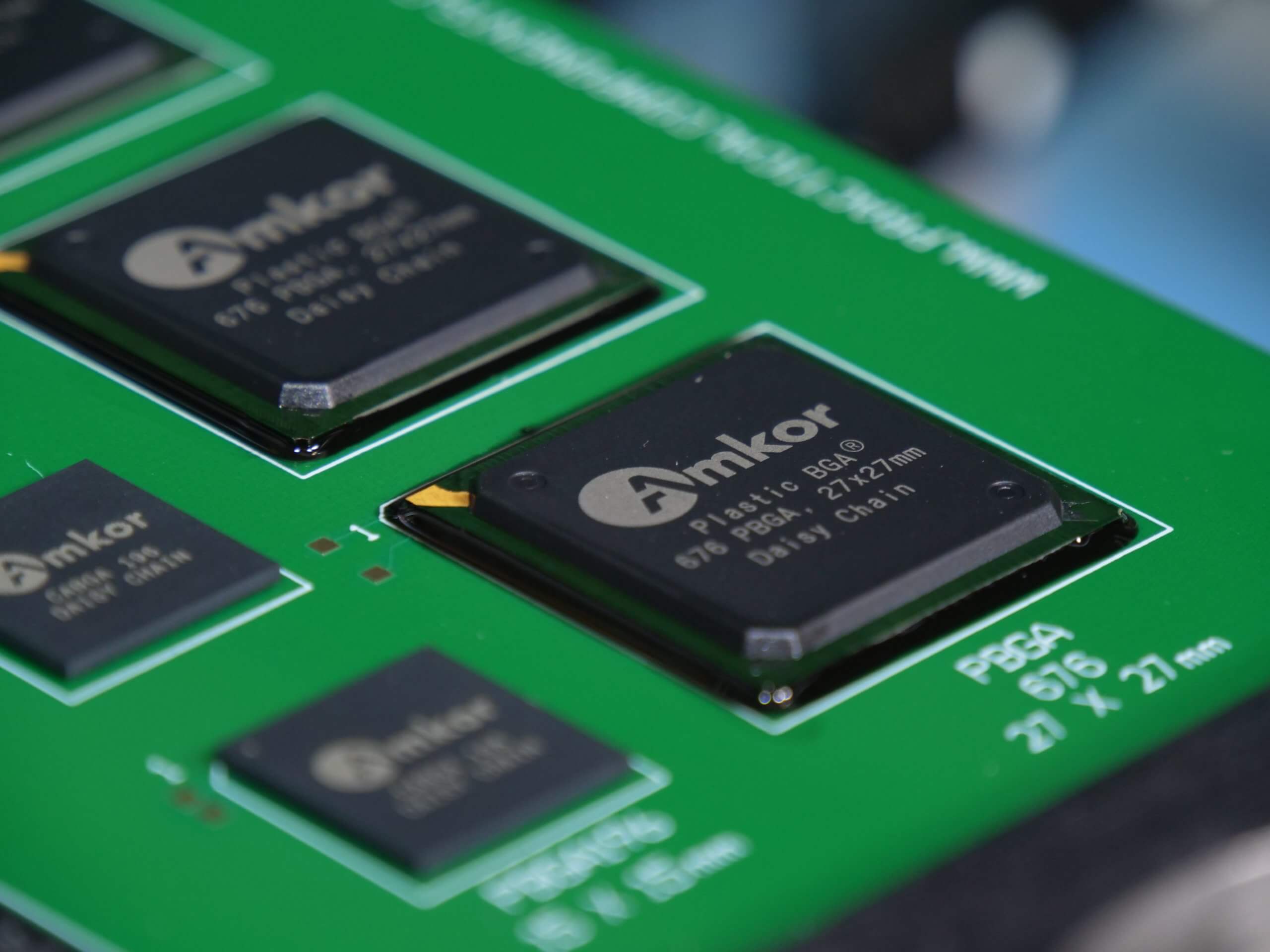
The SCS PrecisionCoat VI selective conformal coating and dispense system is a fully programmable, multi-purpose system that offers unparalleled programming for automated material applications. In addition to coating application, the PrecisionCoat’s multi-valve technologies enable the application of underfill materials, and its potting platform automates the potting process to increase production accuracy and efficiency. Underfill and potting are both used for specific purposes in electronics manufacturing and are applied through distinct processes.
Underfill Applications
Underfill is a composite material made of an epoxy polymer with significant amounts of filler. Additional components like flow agents, adhesion promoters and dyes are also added to the underfill formulation. Consumer electronics, semiconductor packaging, automotive, cell phone and artificial intelligence applications typically employ underfill as their demands require higher performance and miniaturization. Underfill protects these electronic devices from shock or thermal cycling and extends product life cycles. Although primarily used for flip-chip devices like handhelds that must pass drop and tumble tests, underfills can also be used with ball-grid arrays (BGAs).
A PrecisionCoat outfitted with the SCS tower jet valve dispenses underfill onto a corner or along the edge of the ball grid array (BGA) or device. The chip and printed circuit board are then heated to a recommended temperature in the range of 125°C to 165°C; the temperature can vary, depending on the manufacturer. At the recommended temperature, the underfill turns into a liquid and flows under the chip. Underfill provides a strong mechanical bond between the circuit chip and the printed circuit board’s connection, protecting its solder joints from mechanical stress while helping transfer heat. Due to the strong bond created, rework may be difficult.
Potting Applications
Potting is a single or two-part material used to protect components from environmental and mechanical damage. Potting materials are commonly epoxies, silicones and polyurethanes. These resins act as both a base material and an activator, serving as a catalyst to create solids from liquid materials. Potting provides electrical insulation properties, thermal stability and chemical resistance to high voltage applications. Potting processes are commonly used in electronic applications like power supplies, switches, ignition coils, electronic modules, motors, connectors, sensors, cable harness assemblies, capacitors and transformers.
Depending on volume and material type, a pumping system can be used to measure and dispense the material. It can be done in single or multiple steps to reduce voiding and ensure consistent filling of the enclosure or device. Two-part materials are metered and mixed in set ratios to ensure complete curing of the material. The PrecisionCoat potting platform can be configured with one head or multiple heads to dispense one or two-part materials. Various dispense techniques can be used to reduce voiding in the cavity, including bottom fill, multi-stage fills or multi-shot applications.
Potting provides reliable, long-term protection from environmental conditions. However, potting does add weight, thickness and complexity to an electronic assembly as a housing is required to contain the potting material. Additionally, two-part compounds often have special process requirements, and potting can be difficult to inspect or rework.
To learn more about the SCS PrecisonCoat and how its versatile platforms can protect your applications, visit scsequip.com.
Global Coverage Issue 97, Fall 2024