Parylene Deposition Process
Parylene Deposition Process
Parylene coatings are applied at ambient temperatures with specialized vacuum deposition equipment. Parylene polymer deposition takes place at the molecular level, where films essentially ‘grow’ a molecule at a time:
- A solid, granular raw material, called dimer, is heated under under vacuum and vaporized into a dimeric gas.
- The gas is then pyrolized to cleave the dimer to its monomeric form.
- In the room temperature deposition chamber, the monomer gas deposits on all surfaces as a thin, transparent polymer film
Because Parylene is applied as a gas, the coating effortlessly penetrates crevices and tight areas on multi-layer components, providing complete and uniform encapsulation. Optimal thickness of the polymer coatings is determined based on the application and the coating properties desired. While Parylene coatings can range in thickness from hundreds of angstroms to several mils, a typical thickness is in the microns range.
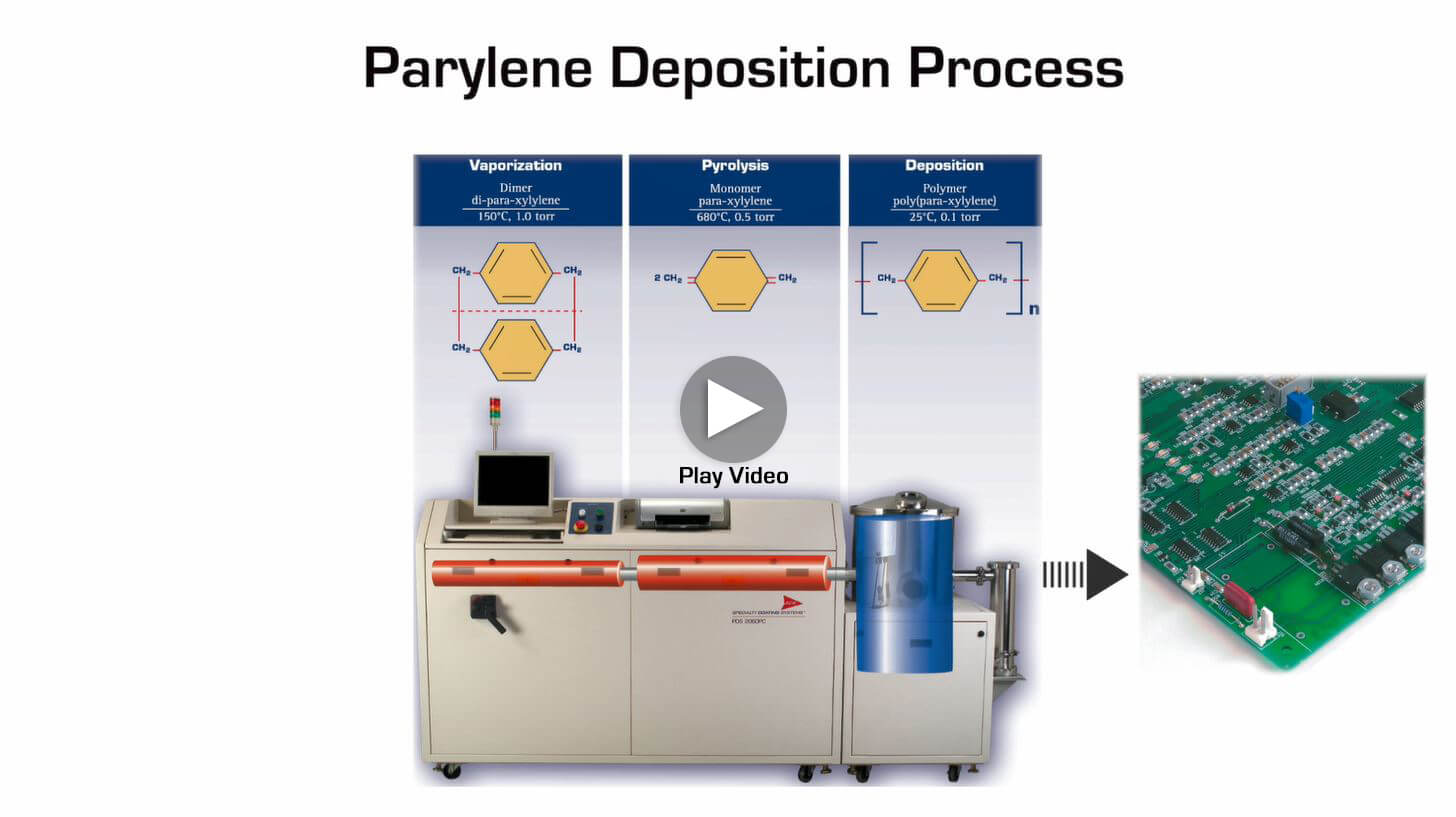
Variables that Influence the Parylene Coating Process
The Parylene deposition process consists of two general parts – the science, explained above, and the ‘art’. The art of Parylene coating is a level of expertise and insight developed over years that helps ensure that Parylene’s protection and performance capabilities are fully and consistently realized. At SCS, the ‘art’ includes a thorough understanding of the variables that can impact coating performance and ultimately the success of your application.
Substrate Material
Optimal adhesion of Parylene to a wide variety of substrates, including metal, plastic, elastomer, glass, paper, etc., is commonly achieved by a treatment with A-174 silane prior to Parylene coating. A few substrates such as highly polished metallic substrates and polymeric substrates, for example, have historically represented adhesion challenges for Parylene. Being on the forefront of Parylene development, SCS has introduced new adhesion promotion technologies that solve a number of these challenges.
Substrate Cleanliness
Proper parylene adhesion to a substrate can be significantly affected by cleanliness. Particulates, manufacturing oils, human oils and other materials not considered a component of the substrate will impact parylene adhesion, performance and reliability. From pre-coat processes to industry-leading cleanroom environments, SCS has established widely accepted standards and processes in this critical area.
Substrate Preparation
One of the Parylene’s defining characteristics is its ability to coat all surfaces, including deep into multi-layers and crevices. As a result, all surfaces in the deposition chamber are coated with Parylene – unless technicians carefully protect, or mask, any areas that are not to be coated. SCS has 50 years of substrate preparation and coating experience, enabling our engineers to draw from a large bank of fixturing and masking techniques to minimize contact points and avoid coating areas that need to remain uncoated.
Repeatable Coating Processes
With highly trained staff, industry-leading deposition systems and robust quality management systems, SCS reliably provides Parylene conformal coatings that, in large production volumes or smaller engineering samples, meet customers’ precise needs – when and where they need it.