Parylene-Abscheidungsverfahren
Parylene-Abscheidungsverfahren
Parylene-Beschichtungen werden bei Raumtemperatur in einer speziellen Vakuum-Abscheidungsvorrichtung via CVD-Verfahren aufgetragen. Die Abscheidung von Parylene-Polymeren erfolgt auf molekularer Ebene, d. h., Folien „wachsen“ genau genommen Molekül für Molekül:
- Ein festes, granuläres Rohmaterial, das als Dimer bezeichnet wird, wird unter Vakuumbedingungen erhitzt und in ein dimeres Gas verdampft.
- Das Gas wird dann pyrolysiert, um das Dimer an seine monomere Form aufzuspalten.
- In der Beschichtungskammer wird das monomere Gas unter Raumtemperatur auf allen Oberflächen als dünner, transparenter Polymerfilm abgeschieden.
Da Parylene in Gasform aufgetragen wird, dringt es bei der Beschichtung von Komponenten mit vielen Lagen mühelos in Spalten und enge Zwischenräume ein und sorgt so für eine vollständige und einheitliche Verkapselung. Die optimale Dicke der Polymer-Beschichtungen wird aufgrund der jeweiligen Anwendung und der erwünschten Beschichtungseigenschaften bestimmt. Die erforderliche Dicke von Parylene-Beschichtungen kann zwischen mehreren hundert Ångström und mehreren Micrometern variieren. Typische Beschichtungen liegen im Bereich von 0,5µm – 75µm.
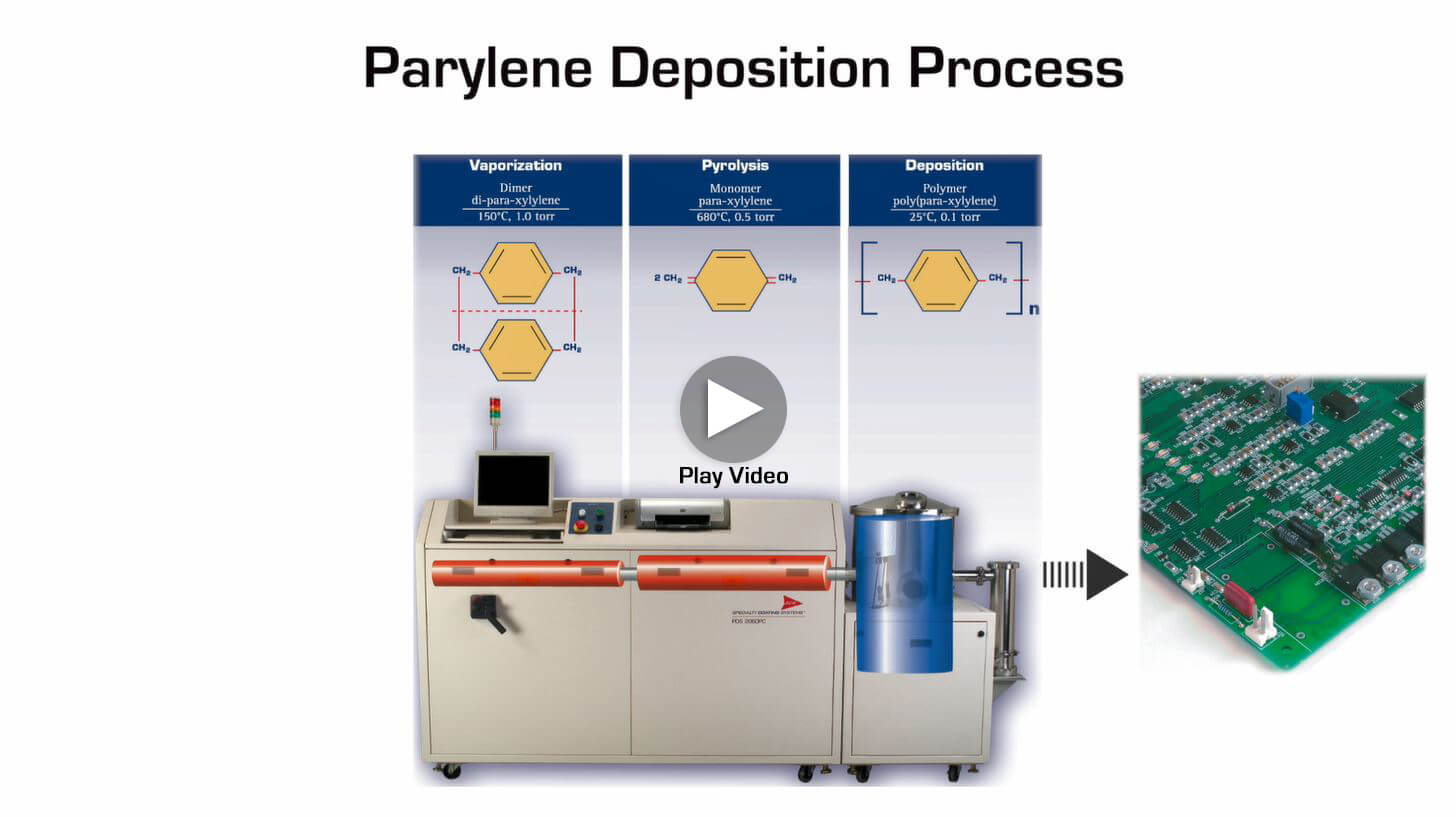
Variablen, die sich auf das Parylene-Beschichtungsverfahren auswirken
Das Parylene-Abscheidungsverfahren beruht einerseits auf den wissenschaftlichen Voraussetzungen, die oben erläutert wurden. Andererseits ist es jedoch auch eine „Kunst“. Umfassendes Know-how und eingehende Erfahrungen, die über viele Jahre gesammelt wurden, bilden die Voraussetzungen für diesen Aspekt der Parylene-Beschichtungen und gewährleisten, dass die Qualitäten und Leistungscharakteristiken von Parylene in vollem Umfang und zuverlässig verwirklicht werden. Bei SCS zeigt sich diese „Kunst“ in dem genauen Verständnis der Variablen, die die Leistungsfähigkeit von Beschichtungen und den letztendlichen Erfolg einer Anwendung beeinflussen können.
Substratmaterial
Die optimale Adhäsion von Parylene auf einer breiten Palette von Substraten, darunter Metalle, Plastik, Elastomere, Glas, Papier und andere Materialien, wird in der Regel dadurch erzielt, dass die zu schützende Oberfläche vor der Beschichtung mit Parylene mit Silan A-174 behandelt wird. Auf einigen wenigen Substraten, wie z. B. auf hochpolierten Metallsubstraten und Polymersubraten, traten bisher Adhäsionsprobleme bei der Beschichtung mit Parylene auf. Als Vorreiter bei der Weiterentwicklung von Parylene hat SCS neue Haftvermittler / Primer eingeführt, die in vielen Fällen Abhilfe für diese Probleme bieten.
Reinheit der Substrate
Die ordnungsgemäße Adhäsion von Parylene auf Substratoberflächen hängt entscheidend von der Sauberkeit ab. Partikel, industrielle Öle, menschliche Öle und andere Materialien, die kein Bestandteil des Substrats sind, beeinträchtigen die Adhäsion, Leistungsfähigkeit und Zuverlässigkeit von Parylene. SCS hat darum für diesen kritischen Aspekt weithin anerkannte Standards und Verfahren entwickelt, die von speziellen Verfahrensschritten vor der eigentlichen Beschichtung bis zu branchenführenden Reinraumumgebungen reichen.
Vorbereitung der Substrate
Eine der charakteristischen Eigenschaften von Parylene ist seine hervorragende Tiefenwirkung auf allen Oberflächen, durch die gewährleistet wird, dass auch tiefere Lagen und Spalten beschichtet werden. In der Abscheidungskammer werden alle Oberflächen mit Parylene beschichtet – es sei denn, es wurden Vorkehrungen getroffen, um bestimmte Bereiche durch Masken oder andere Schutzvorrichtungen von der Beschichtung auszunehmen. SCS verfügt über 50 Jahre Erfahrungen in der Vorbereitung und Beschichtung von Substraten. Unsere Ingenieure können darum auf ein breites Repertoire an Fixierungs- und Maskierungsmethoden zurückgreifen, um Kontaktpunkte zu minimieren und die Beschichtung von bestimmten Bereichen zu verhindern.
Prozesssicherheit des Beschichtungsverfahren
Ein hervorragend ausgebildeter Mitarbeiterstab, branchenführende Abscheidungssysteme und robuste Qualitätskontrollen gewährleisten, dass die konformen Parylene-Beschichtungen von SCS exakte Kundenanforderungen in jeder Hinsicht zuverlässig erfüllen. Gleichgültig, ob es sich um große Produktionsvolumen oder kleinformatige technische Muster handelt – unsere Kunden erhalten präzise, termingerechte Resultate.