Parylene Coating Deposition Process
Understanding the Parylene Coating Deposition Process
The Parylene coating deposition process applies Parylene at ambient temperatures using advanced vacuum deposition equipment. The Parylene polymer is deposited at the molecular level, allowing the film to ‘grow’ one molecule at a time. This scientific process enables the Parylene coating to deliver optimal protection and performance for various applications.
Steps in the Parylene Coating Process:
Vaporization: The process begins with heating a solid, granular raw material known as dimer under vacuum conditions until it vaporizes into a dimeric gas.
Pyrolysis: The dimeric gas is then subjected to pyrolysis, which breaks down the dimer gas into its monomeric form.
Deposition: The monomer gas is introduced into a room-temperature deposition chamber, where it deposits uniformly onto all surfaces to form a thin, transparent polymer film.
One of the unique benefits of Parylene coating is its ability to penetrate deep into crevices and intricate areas of multi-layer components, providing complete and uniform encapsulation. The thickness of the Parylene coating can be tailored to meet specific application needs, ranging from hundreds of angstroms to several mils, though typical thickness is in the micron range.
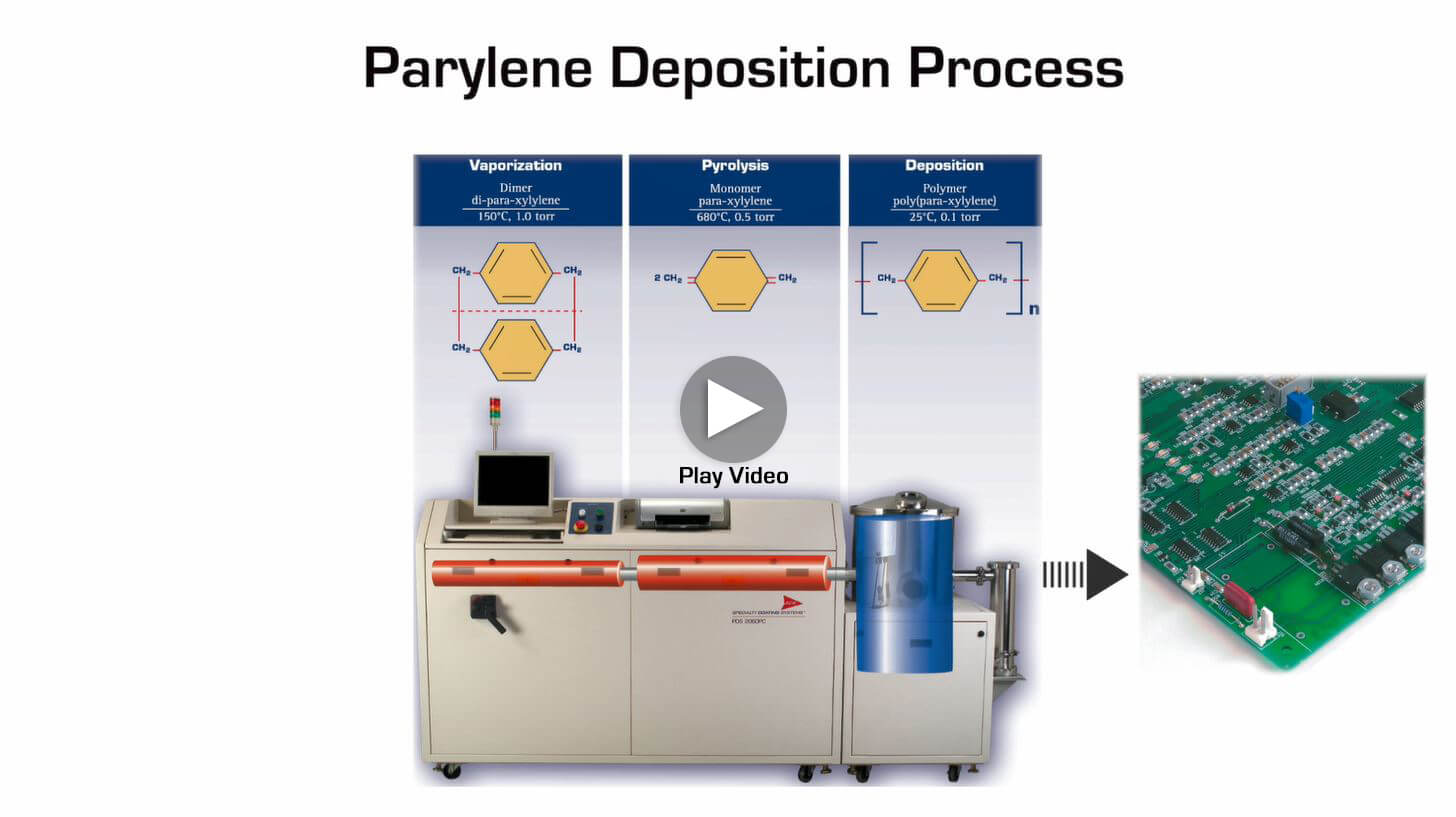
Factors Influencing the Parylene Coating Process
The Parylene coating deposition process requires an understanding of scientific principles and technical expertise. SCS’ experience and understanding of the Parylene coating process ensures consistent delivery of coatings that meet the highest standards of protection and performance. Throughout the Parylene coating process, SCS carefully considers several key variables, including:
Substrate Material:
Achieving optimal adhesion of Parylene coatings to various substrates—such as metal, plastic, elastomer, glass and paper—often requires surface treatments like A-174 silane. Certain materials, such as highly polished metallic and polymeric substrates, among others, can present adhesion challenges and benefit from advanced adhesion technologies. SCS engineered such adhesion promotion technologies that effectively address these challenges.
Substrate Cleanliness:
The cleanliness of the substrate is crucial for proper Parylene coating adhesion. Contaminants like particulates, manufacturing oils and human oils can significantly impact the adhesion, performance and reliability of the coating. SCS adheres to strict cleanliness standards, utilizing pre-coat processes and state-of-the-art cleanroom environments to ensure high-quality results.
Substrate Preparation:
Parylene coatings are known for their ability to coat all surfaces, including deep crevices and multi-layered components. To protect areas that should remain uncoated, SCS employs precise fixturing and masking techniques, drawing on over 50 years of experience in substrate preparation and coating.
Repeatable Coating Processes:
With a highly trained staff, industry-leading deposition systems and robust quality management practices, SCS consistently provides Parylene coatings that meet customers’ specific needs, whether in large production volumes or small engineering samples.