<< View SCS Blog
Enhancing Performance and Reliability of Automotive Electronics
High-tech electronic systems increasingly regulate functions of today’s automobile. Examples of management functions include battery management systems, engine control unit (ECU), emissions controls, fuel systems, fluid monitoring, lighting and powertrain mechanics, which are frequently comprised of miniaturized, multi-layer microelectrical mechanical systems (MEMS)/nano packages. The risk of system failure in hostile vehicular environments due to condensation, corrosive fluids and vapors, excessive temperatures, humidity and prolonged UV exposure is greatly reduced by the use of a protective conformal coating.
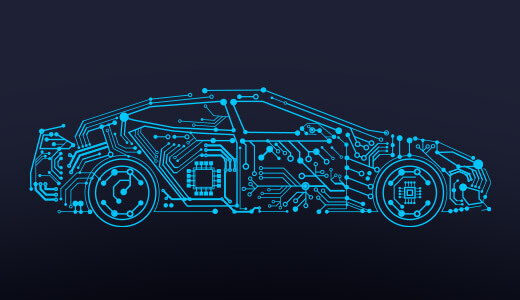
Many conformal coatings exhibit some degree of physical flexibility and protection against mechanical/thermal shock while safeguarding the component from exposure to corrosive elements. Understanding the environment of the end automotive system is key to selecting the best conformal coating for an automotive printed circuit board (PCB) or component application.
The cost-effectiveness of a device or system can actually be enhanced by making initial investments in solutions that will work without replacement or repair in the longer-term. Wet coatings like acrylics, epoxies, silicones and urethanes offer simple application and relatively easy removal, repair and replacement. In contrast, Parylene’s specialized vapor deposition process can be a slower process and, at times, comes with a higher cost. However, because Parylene is applied as a gas, it penetrates far deeper into the substrate surface and generates the highest levels of protection available for many automotive purposes. Parylene coatings are a superior substrate covering for automotive PCBs, providing durable, ultra-thin protection for strategically-situated moving parts and related electro-mechanical assemblies.
Expanded Automotive Use of Parylene Conformal Coatings
As an electrical insulator, Parylene provides long-term surface insulation resistance (SIR) which stimulates optimal function of automotive systems, including:
- ECU
- Battery management systems (BMS) electronics and cooling components
- Analytical performance measurement of automotive systems’ functioning
- Torque sensor
- Anti-lock brakes control
- Emissions management
- Instrument pods circuitry (IPC)
- Power controls/modules for doors, mirrors, seats, sunroof and windows
- Power train/chassis operations
- Passenger comfort/convenience
- Tire-pressure gaskets/seals
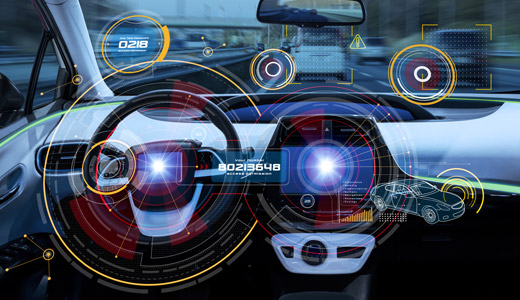
When protected with Parylene polymer films, PCBs and related components benefit from enhanced functional integrity, despite ongoing exposure to operational ecosystems characterized by the presence of acidic substances, chemical contaminants, fluctuations of electrical current, humidity, moisture, temperature changes or a mixture of these conditions. Providing chemical, dielectric and moisture protection that far surpasses many conformal coatings, Parylenes are a conformal coating of choice for numerous applications and functions:
- PCBs in new automobiles contain approximately 100 million lines of code and have advanced circuitry with scores of microprocessors. Parylene coatings’ excellent dielectric properties provide insulation that permits PCB traces to be situated closer together, reducing the potential for nearby electronics interfering with performance and also diminishing component size.
- MEMS manage signal-processing and communication functions in electronic vehicular systems. Manifold air pressure (MAP), manifold air temperature (MAT) and power train/chassis control are regulated by MEMS sensors. Frequently situated in areas of high-performance activity and stress, MEMS sensor maintenance is essential to assure safe, efficient automotive performance. Of the different types of conformal coatings, Parylene best safeguards micro-machined circuits from the potentially harmful effects of aggressive automotive environments.
- Ruggedization of automotive components and systems stabilizes performance through exposure to BMS cooling fluids, harsh engine fluids, high levels of vibration and temperature extremes. Parylenes provide stability for delicate components exposed to vibrations and shock/internal disruption within the engine for numerous automotive systems, including detection/door switches, environmental protection monitors, mechanical/physical performance gauges, motion controllers and components regulating safety, rocker and tactile functions.
- LEDs are increasingly being used across automotive and transportation applications. Parylene conformal coatings extend the functional life of LED electronics, improving performance and ensuring long life.
- Elastomer/polymer seals normally confronted by harsh operating conditions benefit from Parylene films, which stimulate enhanced operational efficiencies and consequent functional upgrades.
Often situated in demanding end-use environments, automotive PCBs, electronic sensors and similar assemblies benefit from application of Parylene conformal coatings. The ultra-thin coatings significantly lessen the likelihood of performance degradation in automotive environments characterized by persistent exposure to corrosive engine liquids and byproducts, winter road-salts, mechanical vibration, noxious exhaust gases and fluctuating thermal conditions.
Continuously-evolving products for automotive information technology, electrical systems, engine components and sensors increasingly depend on Parylene coatings to ensure reliable performance through harsh operating conditions. For more information on protecting automotive electronics with Parylene conformal coatings, call 1-317-244-1200 or contact SCS online.
Global Coverage Issue 93, Fall 2022