<< View SCS Blog
Eliminating PFAS Concerns in Balloon Catheter Manufacturing with Parylene-Coated Mandrels
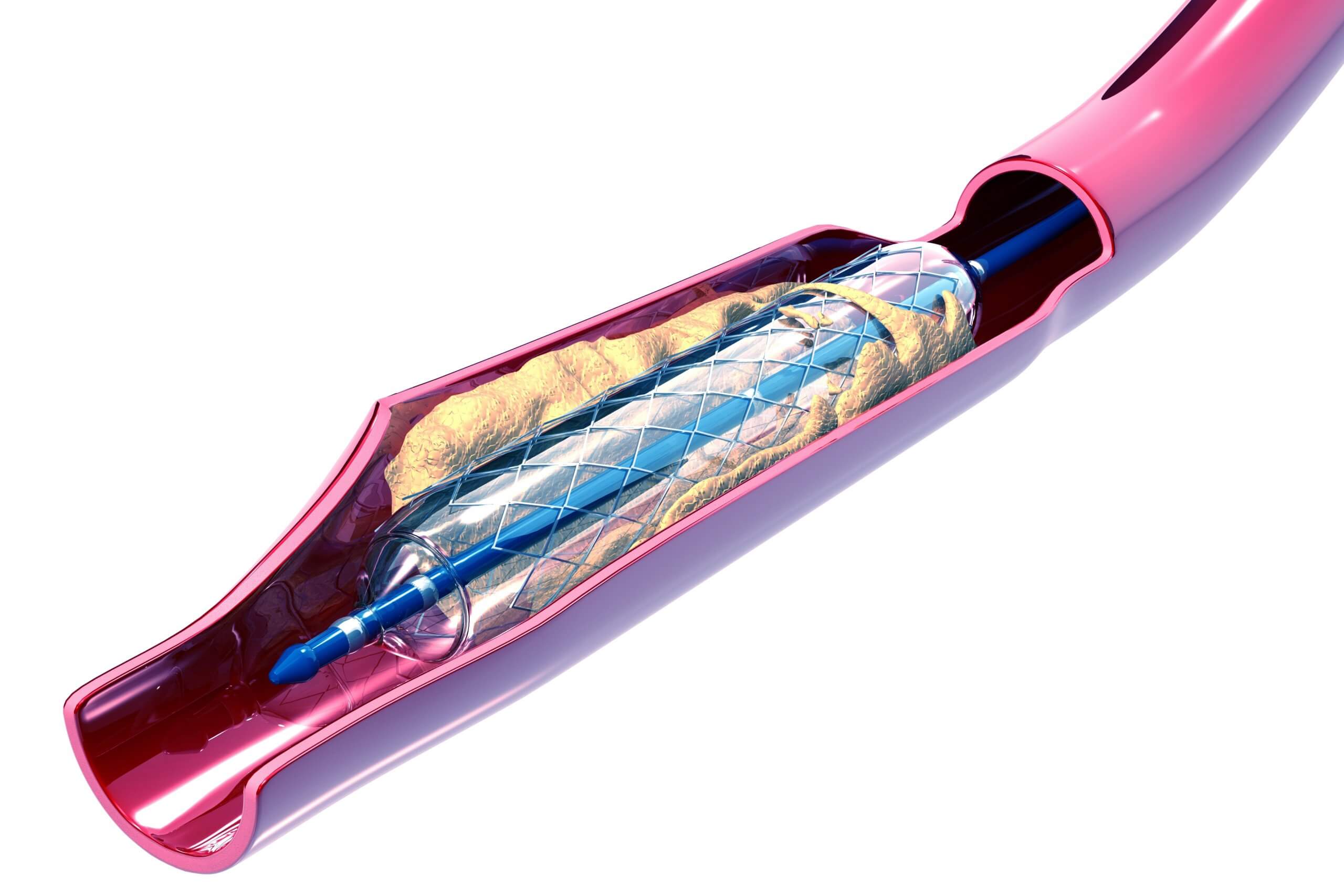
The reliable manufacture of balloon catheters is a key process behind a number of critical medical treatments that include balloon angioplasty, stent and drug delivery, transcatheter aortic valve implantation, atherectomy, renal denervation and laser balloon angioplasty, among others. These minimally-invasive procedures have greatly improved quality of life, increased patient safety and recovery times, and lowered treatment costs.
A balloon catheter consists of a polymer balloon is attached to a catheter at each end of the balloon. The bond made between the balloon and catheter requires heat sealing via direct thermal compression, RF welding or laser processing. In each case, the process requires a hard surface to form inside the catheter/balloon pair in order to achieve a strong, reliable bond that is able to contain the high inflation pressures required during use. A precisely-sized, wire-forming mandrel is inserted through the catheter and the overlapping balloon in order to stage the assembly for sealing.
These wire-forming mandrels range from a few inches to 120 inches in length and are typically fashioned from medical-grade stainless steel with highly-specialized varieties made from other exotic alloys, including the shape memory alloy known as Nitinol. After completion of the bonding process, these mandrels must be withdrawn from the assembly without sticking or damaging the new bond. This removal process is facilitated through the use of a permanent release coating on the mandrel, generally comprised of either a Parylene or polytetrafluoroethylene (PTFE) conformal coating.
While both Parylene and PTFE have similar cost and performance, and have been successfully used for decades, increasing concerns have been highlighted regarding the use of fluorinated polymers for both direct and indirect human exposure. Collectively called PFAS materials, PTFE is a subgroup that makes up a large portion of the PFAS market. Conversely, the most common Parylene variant used on mandrels is Parylene N, which contains no fluorine or other halogens.
With its proven track record on mandrels, manufacturers utilizing PTFE-coated mandrel wires may choose to circumvent potential PFAS concerns by turning to Parylene, a reliable and proven solution. As a vacuum-deposited conformal coating, Parylene provides critical release capabilities in an ultra-thin, highly-uniform film. Additionally, Parylene is advantageous due to its ability to uniformly coat the complex wire shapes and configurations that are becoming common in advanced catheter technologies.
If you would like more information about SCS medical conformal coating services, contact SCS online or call +1.317.244.1200.
Global Coverage Issue 96, Fall 2023