<< View SCS Blog
Enhancing Avionics Reliability with Conformal Coatings
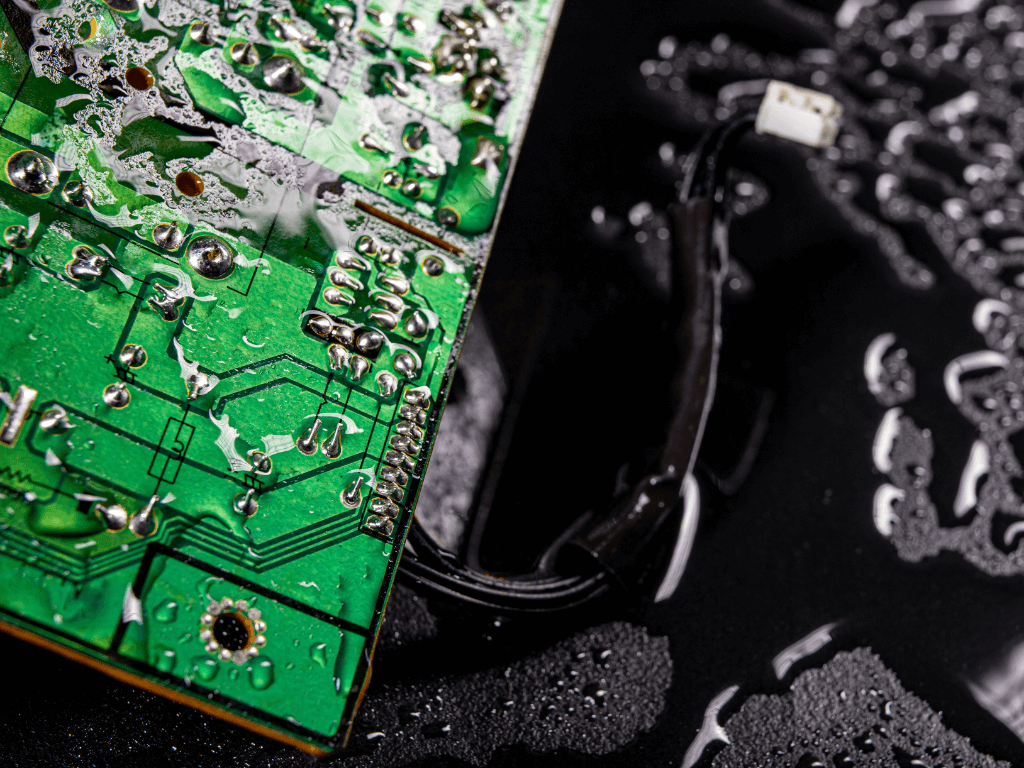
The aviation industry has experienced significant growth in the integration of electronic systems into modern aircraft. These systems include a complex network of sensors, processors and communication modules that enhance safety and efficiency. They perform critical functions that range from navigation and communication to in-flight entertainment and monitoring. As aircraft become increasingly reliant on these electronic systems, ensuring their dependability and protection is crucial. One of the most effective methods for safeguarding these systems is the application of conformal coatings.
Aircraft electronics are exposed to various environmental stressors, including temperature fluctuations, high humidity, corrosive chemicals, dust and vibration. Ambient temperatures experienced by aircraft components range from -65°F (-55°C) at 35,000 feet to 110°F (43°C) or more on land and can rise further in various parts of the aircraft during operation. Additionally, moisture intrusion or contamination by saltwater and mechanical fluids can degrade electronic circuits, leading to malfunctions or failures. To address these issues, manufacturers are increasingly turning to conformal coatings as a protective solution. These coatings provide robust barriers that ensure the longevity and reliability of electronic components in demanding operating conditions.
Conformal coatings are thin, protective films applied to printed circuit boards (PCBs) and other electronic components to safeguard them from environmental hazards. These coatings conform precisely to the contours of the components, forming a protective layer without compromising functionality. The primary types of conformal coatings include:
- Acrylics (AR): Known for their ease of application and reworkability, acrylic coatings offer excellent protection against moisture and humidity.
- Silicones (SR): Silicone coatings excel in high-temperature applications and offer excellent flexibility, making them suitable for aircraft electronics exposed to thermal cycling.
- Urethanes (UR): These coatings provide superior resistance to chemical exposure, abrasion and other types of mechanical wear, making them ideal for harsh environments. However, Urethanes do not withstand high temperatures, as they commonly break down at temperatures above 125°C.
- Epoxies (ER): Known for their strong adhesion and chemical resistance, epoxy coatings are used in applications requiring high mechanical strength.
- Parylenes (XY): These are vapor-deposited polymer coatings that provide excellent moisture and chemical barrier properties at thin, lightweight levels. Additionally, Parylenes offer high dielectric strengths and low dielectric constants, making the coatings excellent electrical insulators. Because of this wide range of beneficial properties, Parylenes are often used in critical aerospace applications.
Protecting avionics with conformal coatings is critical for the reliability and performance of modern aerospace technology. Innovative protective solutions can significantly reduce maintenance costs, improve safety and extend the lifespan of avionics systems. As aerospace technologies advance, the need for robust and efficient protective measures will continue to grow.
To learn how conformal coatings can protect your aerospace electronics in harsh environments, contact SCS.
Global Coverage Issue 101, Winter 2025