<< View SCS Blog
Conformal Coatings Shield Marine Electronics in Harsh Environments
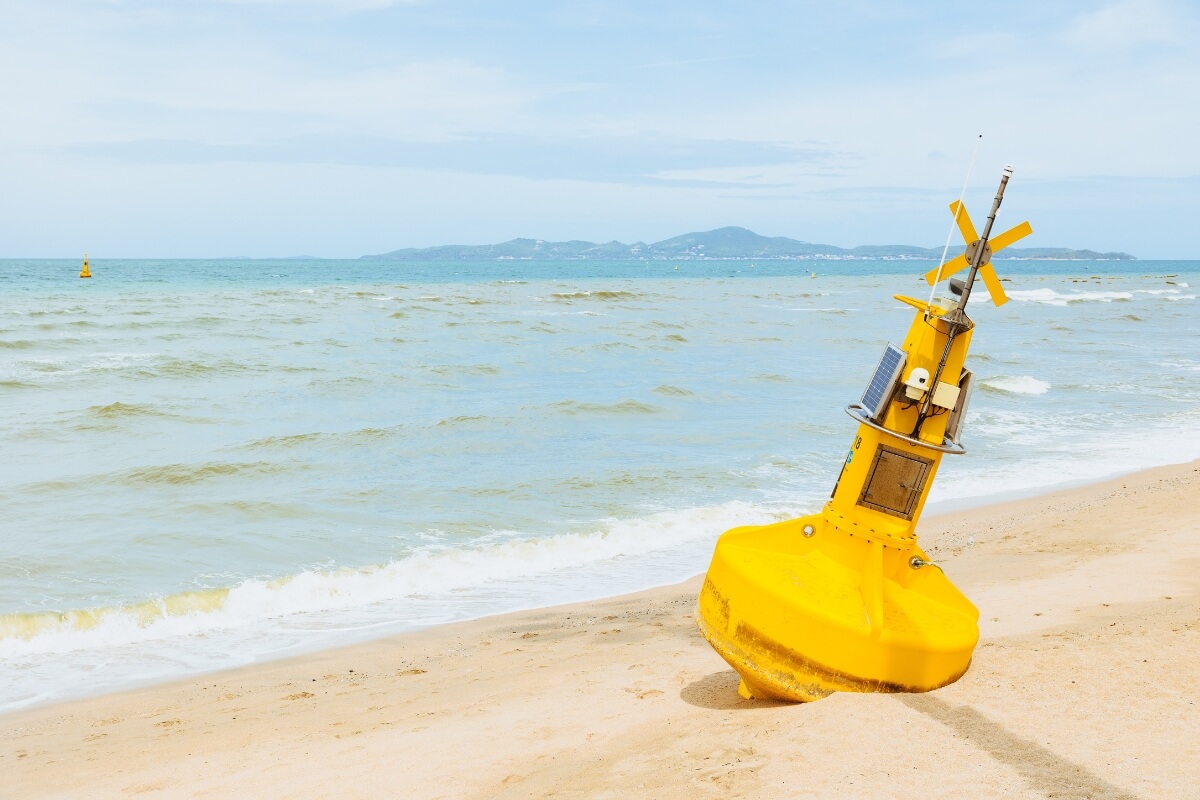
Marine electronics endure some of the harshest environmental conditions on the planet and those conditions threaten their longevity and performance. Relentless saltwater exposure can cause moisture ingress and corrosion, which can lead to short circuits. Extreme temperature fluctuations result in thermal stress, and vibration and mechanical shock induce breakdowns in electronic systems. Protective conformal coatings can ensure the reliability of critical marine electronics like underwater sensors, radar systems, GPS and positioning systems as well as biological detection systems.
Underwater sensors are used for a wide range of purposes from environmental monitoring to underwater exploration. Vital for navigation and security in marine operations, radar systems rely on conformal coatings for enhanced performance, improved signal clarity and reduced maintenance. GPS and positioning systems have also shown improved reliability and longevity due to conformal coatings. Maintaining precise positioning and navigation capabilities are essential for safe and efficient marine operations.
Missile defense systems also require precise and dependable electronics to ensure accurate targeting and response capabilities. Conformal coatings help maintain their integrity by protecting critical components from environmental factors such as humidity, temperature fluctuations and physical shock.
Finally, biological detection systems are essential for monitoring aquatic ecosystems and detecting potential threats. The application of conformal coatings protects these sensitive electronics from moisture and contaminants, enhancing their operational reliability and allowing for more accurate and timely data collection.
Effective Coating Solutions for Marine Electronics
Various conformal coatings have proven their efficacy in safeguarding sensitive components from the rigors of marine environments.
- Polyurethane, long valued for its high flexibility and resilience against moisture and UV exposure, forms a durable bond with electronic substrates, providing a reliable moisture barrier that is critical in preventing corrosion.
- Silicone-based coatings have gained prominence due to their exceptional thermal resistance and ability to withstand extreme humidity and temperature variations. Their inherent hydrophobic properties effectively repel water, minimizing the risks associated with moisture ingress and making silicones ideal for use in underwater sensors and radar systems.
- Epoxies have played a significant role in the protection of marine electronics, offering outstanding mechanical strength and adhesion capabilities. Their versatility allows for customization in viscosity and curing time, making them suitable for multiple applications. Advancements in formulations have led to epoxy coatings specifically engineered to provide not only physical protection but resistance to chemical degradation caused by seawater immersion.
- Parylene conformal coatings provide exceptional moisture barrier properties and resistance to chemicals to enhance the durability of electronic systems that are exposed to corrosive saltwater and extreme humidity. Applied through a vapor deposition process, Parylene’s room temperature application process allows for compatibility with heat-sensitive components, extending the product life and reliability of devices operating in challenging marine conditions. Parylene has been integral in enhancing the performance of critical systems like sonar, communication devices and navigation equipment.
In an industry where reliability and performance are paramount, conformal coatings offer an essential layer of protection for marine electronics. By shielding these systems from moisture, corrosion and other environmental hazards, conformal coatings significantly enhance longevity and functionality.
For more information on how conformal coatings can protect your marine electronics applications, contact SCS.
Global Coverage Issue 99, Summer 2024