SCS Blog
Recent SCS Blogs
Best Coating for Dielectric Strength
Dielectric strength, also known as voltage breakdown strength (Vbd) is a measure of a conformal coating’s electrical insulation effectiveness. Higher values are often key to success for design engineers, and when it comes to conformal coatings, those with hydrophobic properties and lower extractible ionic impurities are less likely to both attract water and render the... Read More >>
Parylene Removal, Rework and Repair
The advantages of Parylene as a conformal coating are widely recognized. It resists heat, cold, moisture and pressure; salt spray, electricity and solvents cannot permeate it. And while these attributes of Parylene contribute to the conformal coating’s appeal, they also present distinct challenges, particularly in regards to Parylene removal, rework and repair. Because of Parylene’s... Read More >>
What if my Conformal Coating is Applied Too Thick?
The thickness of conformal coating plays a vital role in the optimal performance of printed wiring assemblies, circuit boards, and electronic devices. An inadequate coating thickness hinders proper coverage, while an excessive thickness can lead to undue stress on solder joints and components, especially glass-bodied ones. Additionally, controlling coating thickness is of great importance with... Read More >>
Lubricious Coatings
Lubricity refers to a conformal coating’s capability to reduce friction during operation, preventing any hindrances to its function that could jeopardize patient well-being. Lubricious coatings offer essential protection for devices such as cardiac-assist devices (CADs), catheters, elastomers, cables guidewires and stents. In contrast to an uncoated device, lubricious films can reduce frictional forces by more... Read More >>
When Not to Use Acrylic Conformal Coating
While acrylic conformal coating does have many benefits, it is not the best solution if an application will be exposed to solvents, needs to withstand high temperatures or requires coating hardness. Solvent exposure Acrylic conformal coating can be removed with a weaker solvent such as isopropyl alcohol or xylene. If the coating encounters even stronger solvents,... Read More >>
Type UR Conformal Coating Examples
Type UR (urethane resin) conformal coatings are a common choice for conformal coating projects because of their resistance to chemical solvents, hardness and moisture protection. Common type UR conformal coatings include: UR conformal coating offers exceptional resistance to chemical solvents, making it ideal for applications exposed to harsh chemicals. Additionally, consider urethane conformal coating for... Read More >>
How to Source Conformal Coating Removal Services
Conformal coatings protect PCBs and ensure they work reliably throughout their expected operational life. However, poor coating application or selection of the wrong coating material can cause assembly malfunction. In other cases, poorly manufactured PCBs may need component repair/replacement. When these problems arise, coating removal is necessary. Removal Methods Removal depends largely on the coating... Read More >>
Sterlization of Parylene
Regardless of the variant, Parylene, is highly acclaimed for the many advantages it offers as a protective conformal coating for medical, aerospace, defense, LEDs, and automotive applications. Chief among the coating’s benefits, however, is that it can withstand common sterilization techniques, such as electron beam (e-beam), gamma, ethylene oxide (EtO), and steam autoclave. Like many... Read More >>
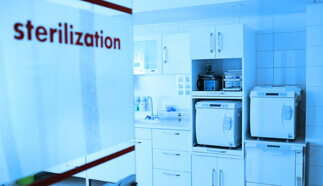
Benefits of Conformal Coatings
Manufacturers in the electronics, transportation, aerospace, defense and medical industries have applications that need to withstand elements of heat, cold, rain, snow, vibration, fungus, oxidation and corrosion through decades of operation. Without protection, their applications would not survive these harsh environments. Conformal Coatings Protect Circuit Boards and Electronic Devices from Their Environments Conformal coatings add a... Read More >>
Parylene Process: 5 Keys to Success
Parylene Process: The basic Parylene variant is Parylene N (poly-para-xylylene). Additional variants of Parylene can be achieved via chemical modification to Parylene N main-chain phenyl ring and its aliphatic carbon bonds. Parylene N’s modification by a functional group such as Chlorine and Fluorine leads to Parylene C (poly (2-chloro-para-xylylene)) and Parylene F, respectively. Derivatization results... Read More >>