SCS Blog
Recent SCS Blogs
Will Parylene Pass a Taber Test?
Taber tests are designed to measure a material’s capacity to withstand abrasion and its effects during operation. Conformal coatings – liquids and Parylene – are used on printed circuit boards (PCBs) and related electrical assemblies to safeguard their function from hostile environments where operational conditions could lead to development of abrasion, arcing, electrical shorting, fungus,... Read More >>
Conformal Coating for Automotive Applications
Parylene is becoming one of the most useful tools in an automotive design engineer’s arsenal. From protecting internal sensors and circuit boards to keeping LED indicator lights bright and color-accurate, Parylene conformal coatings are an important part of protecting today’s sensitive automotive electronics. Parylene Basics Parylene is a unique conformal coating in that it gets... Read More >>
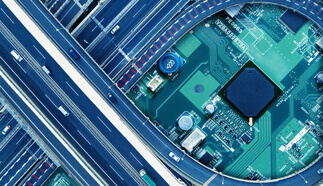
How Thick should Silicone Conformal Coating be Applied?
Silicone conformal coating is commonly used because of its excellent moisture resistance, short cure time and high temperature capabilities. It is also one of the easiest conformal coatings to work with. In order for the coating to function optimally, it has to be applied at the proper thickness. Maintaining appropriate thickness is critical for silicone... Read More >>
The Cost of Parylene Coating vs. Other Conformal Coatings
Parylene is widely regarded as the ultimate conformal coating for safeguarding devices, components, and surfaces in various industries due to its exceptional ability to prevent the infiltration of gases, liquids, or radiation onto circuit board components. The perceived cost of Parylene is a problem, however. This article will explore the cost of Parylene when compared... Read More >>
Can I Spray Parylene Myself?
Can I spray Parylene myself? Can Parylene even be spray coated? The short answer to both of these questions is no. Let’s take a look at Parylene’s chemistry and physics to understand why. Polymerization Type and Process For Parylene film to be formed and subsequently serve as a conformal coating, the dimerized starting material must... Read More >>
What Causes Bubbles In Conformal Coating?
A major causes for failure during conformal coating inspection is bubbles. Bubbles are trapped pockets of air under coating that can cause voids. The 6 Leading Causes of Bubbles: SCS is the world leader in conformal coating services and technologies with more than 50 years of application and engineering expertise. To discuss your application, call... Read More >>
Managing the Conformal Coating Process
Managing the conformal coating process begins with a precise definition of coverage required. Pre-process discussions need to take place to clarify coating requirements and agree whether the coating is needed on metallic or hermetically-sealed regions of the assembly, as well as coverage below/beneath components, or on the backside of electronic leads. Understanding these conditions prior... Read More >>
Dielectrical Performance and Strength of Parylene
A primary function of all conformal coatings is maintaining sufficient insulation and avoiding dielectric breakdown while protecting printed circuit boards (PCBs) and related electronic assemblies. Providing a completely homogeneous coating surface, Parylene (XY) conformal coatings are exceptionally corrosion-resistant, dense and pinhole-free. Among other performance advantages, ultra-thin XY protective films offer superior dielectric properties. Dielectric substances... Read More >>
Silicone Conformal Coating offers Many Benefits
Silicone conformal coating is gaining traction as a preferred choice for various applications. Its high temperature resistance, moisture protection, and ease of application and rework make it an ideal option for numerous projects. Most silicone coatings have a continuous operating temperature rating of 200ºC. This is much higher than Parylene N (80ºC) and acrylic (125ºC)... Read More >>
Is Conformal Coating Necessary for PCBs?
When designing a product or system, the PCB is one of the most critical components, supporting main functions like power supply and communication. It is key to maximize the PCB’s working life and protect it from harsh environments. Conformal coating provides PCBs the protection needed to endure various conditions and work reliably. Utilizing conformal coating... Read More >>
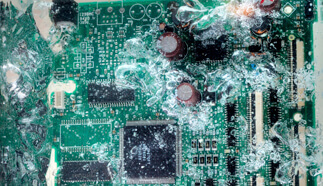