SCS Blog
Recent SCS Blogs
Parylene Variant Comparison
Parylene and Its Uses Depending on the specific use, Parylene conformal coatings can be effective in film thickness ranges of 0.1 – 50 microns, far finer than competing coating materials. Parylene’s other beneficial qualities include these multiple capabilities: In addition to consumer and industrial products, conformal coatings have a wide range of military, aerospace, medical biocompatible... Read More >>
When to Use Urethane Conformal Coating
Urethane conformal coatings are an excellent choice for many conformal coating projects. Their ability to resist chemical solvents, address tin whiskers effectively, and offer remarkable durability, makes them a preferred choice in the realm of conformal coatings. Chemical ResistivityUrethane resin conformal coatings exhibit exceptional resistance to chemical solvents. Applications needing prolonged protection against harsh solvents should... Read More >>
Parylene Adhesion & Cleaning
Parylene conformal coatings provide effective chemical, electrical, moisture and vapor protection for complex electronic circuit assemblies made to maintain performance throughout demanding operational circumstances. Parylene’s effective adherence to the substrate’s surface is imperative if its many benefits are to be realized. Mechanical methods of adhesion promotion must be employed to ensure Parylene appropriately adheres to substrate surfaces. Surface... Read More >>
What Happens to Parylene when the Dielectric Voltage is Exceeded?
Parylenes, derived from poly(para-xylylene), serve as conformal coatings across diverse sectors like automotive, medical, electronics, military and semiconductor industries. They are inert, transparent and have excellent barrier properties as dielectric thin films. Because their deposition takes place under vacuum, sub-micron range crevices can be coated leading to excellent barrier properties (void free) and they have... Read More >>
What is the Maximum Object Size for Parylene Coating?
While there are many components that can be coated with Parylene, there are some limitations. One of these limitations is size. The actual application of Parylene during the vapor deposition process (VPD) occurs in a deposition chamber. Therefore, the object to be coated must fit in this chamber. Chambers range in size to accommodate a variety of... Read More >>
Parylene Coating vs Conformal Coating
Conformal coatings consist of various polymeric materials used to protect the function and extend the life of electrical and mechanical circuitry, parts and related components. They safeguard parts and products from environmental contamination during use, insulating the substrate while doing so. To achieve this goal, ultra-thin layers, usually just a few millimeters thick, are meticulously applied... Read More >>
Parylene Conformal Coating for Medical Use
Parylene conformal coatings have protected medical device components with an extended range of applications for 50 years. They offer both patients and medical personnel a highly reliable level of uniform, biocompatible protection on components that range from the simple to the highly complex. Their value and application will continue to proliferate, as technology develops. Organic Polymers... Read More >>
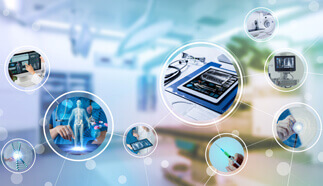
Tubing and Parylene Coating
Tubing is designed to contain or transport substances, typically liquids or gases, and is often constructed of plastic, metal and sometimes glass. When many people think of tubing, they envision its use in construction or mechanics, which is often specified by its material of construction as well as its dimensions, specifically OD (outer diameter) and... Read More >>
Moisture Protection of Parylene
Conformal coatings play a vital role in safeguarding the performance of advanced electronics, like printed circuit boards (PCBs), ensuring their functionality under demanding conditions. A key focus of these coatings is shielding PCBs from moisture damage, which can stem from various sources. Exposure to acid rain, harsh solvents, air pollutants, chemicals, fog, high humidity, intermittent... Read More >>
How to Avoid Bubbles in Conformal Coating
Bubbles and foam are two of the leading causes of failure during conformal coating inspections. Bubbles cause voids in the coating, leaving areas of the substrate exposed to potential contaminants. Therefore, it is important to understand what causes bubbles to form and the steps to take to prevent them. 5 Common Causes of Bubbles in... Read More >>