<< View SCS Blog
Coating Spotlight: SCS Acrylic Conformal Coatings
Defined by IPC-CC-830 as Type AR, acrylic conformal coatings are some of the most widely used coatings in the market today. Acrylic coatings provide strong moisture protection, are generally easy to apply and come at a relatively low cost point. While there are numerous formulations available, a few well known acrylic coatings include HumiSeal® 1B31, Humiseal1B73, MG Chemicals 419C and Electrolube APL.
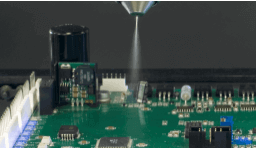
Similar to other liquid conformal coatings (e.g, Type UR, ER, SR, etc.), acrylics can be applied via manual or automated spray, brush or dip methods. Many acrylics cure in as little as 30 minutes at room temperature, making them an attractive option for high-volume or quick-turn applications. In addition, acrylics are one of the easiest coatings to remove if component rework is frequently required.
While acrylics have many advantages, the coatings also have a few drawbacks to take into consideration. For example, the ease of reworking acrylic coatings is offset by their inability to withstand harsh solvents. Thus, if a coated application will be used in an environment that includes exposure to solvents, using Parylene or urethane conformal coatings might be a better solution. Furthermore, most acrylics can withstand temperatures up to 125°C; if an application’s operating environment exceeds that temperature, an alternate coating should be evaluated.
Acrylic conformal coatings have found great success in the electronics manufacturing industry due to their ease of application, strong moisture protection, relative low cost and ability to be reworked. To learn more about acrylic conformal coatings and how they can protect your applications, contact Sean Horn at 814.535.3505, ext. 1802, or shorn@scscoatings.com.
Global Coverage Issue 91, Spring 2022