<< View SCS Blog
What is the Service Life of Parylene?
Under ambient conditions (room temperature, in air) Parylene is a lifetime conformal coating. Exposure to environmental stressors like temperature, oxygen, UV-light and chemicals can degrade the lifetime, especially when two or more are present at the same time.
Grattan and Bilz, reported that the useful lifetime of Parylene as a conformal coating at 25°C (room temperature) without light exposure is 2,200 years for Parylene N, and 130,000 years for Parylene C [1]. Thermal endurance values of Parylene N, C and D are summarized in Figure1 [2].
Tensile Strength and Thermal Endurance: Free-standing Parylene films have been evaluated by tensile testing, with a 50% loss in the tensile strength used as the failure criterion. In the degradation of many polymers, including the Parylenes, tensile strength is maintained until chain scission has reduced molecular weight to the point at which entanglement is no longer a factor in determining physical properties. Beyond that point, it drops abruptly. Thus, the 50% loss criterion allows a reasonably precise location for end of useful life on a log time scale (Fig 1).
Parylene HT®, one of the newest variants of Parylene, has the longest stability, followed by Parylenes D, C and N. Once these films are exposed to damaging UV rays, the useful lifetime of Parylenes D, C and N decreases further due to oxidation and the molecular chains absorb oxygen and form carbonyl chains. Researchers suggest that quantification of oxidation products is possible and the consumption of oxygen leads to an increase in the spectrum fingerprint of carbonyl peak (1700cm-1 for Parylene N and 1695cm-1 for Parylene C). The rate of oxidation decreases in time, likely due to the decrease for chains available for oxidation. The degradation becomes inevitable under these conditions and the pinhole-free nature of the film becomes compromised. As Parylene films become increasingly oxidized, yellowing and embrittlement can occur. This was observed by researchers who reported that the onset of yellowing occurred first with Parylene N, then Parylene C [1].
Parylene HT exhibits outstanding survival at higher temperatures and UV-exposure, replacing the CH2-CH2 (methylene-methylene) connecting bonds between the benzene rings of Parylenes N, C and D with CF2-CF2 bonds, significantly enhancing its high temperature stability. Continuous use of Parylene HT is acceptable at temperatures as high as 350°C, with short-term excursions up to 450°C.
25°C | 60°C | 100°C | 150°C | |
Parylene HT | Longer | Longer | Longer | Longer |
Parylene D | Longer | Longer | 10 years | ˂1 day |
Parylene C | 130,000 years | 15 years | ˂1 year | ˂˂1 day |
Parylene C UV exposure | 2.34 years | |||
Parylene N | 3,880 years | 10 years | ˂1 month | ˂˂˂1 day |
Parylene N UV exposure | 0.31 years |
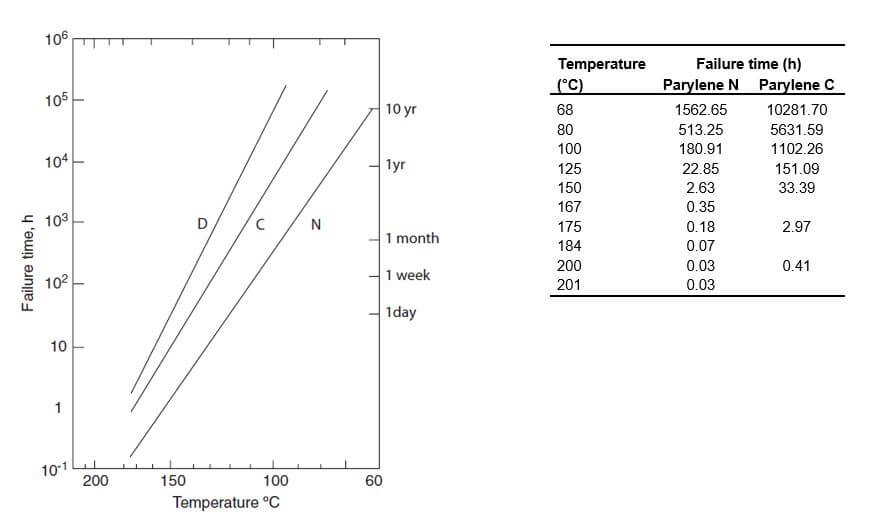
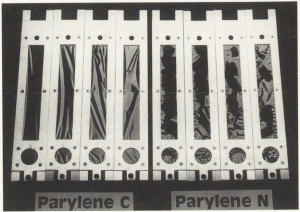
The effect of UV exposure and Lifetime: Grattan and Bilz later carried out another study on Parylenes C and N to measure the effect of UV light exposure on film oxidation. They set 0.061 M carbonyl concentration as the criterion for film failure. Their findings indicated that under UV exposure of 2500 lux Parylene N can withstand 2784 hours (0.31 years) and Parylene C can withstand 20,538 hours (2.34 years) at room temperature (Figure 2) [3]. This is consistent with accelerated weathering tests completed on the Parylenes that evaluate film appearance on a standardized scale.
There is a significant difference between the failure time of UV exposed films compared to films that are not exposed. This provides guidance regarding the proper service conditions of Parylene C and N, as well as vital information regarding when Parylene HT becomes the optimum choice. The chemical structure of Parylenes N, C, and D are susceptible to degradation via heavy UV exposure. Conversely, the chemical structure of Parylene HT defines its ability to withstand long-term exposure to UV. The same CF2-CF2 bond replacement between repeating units is responsible for the vastly improved UV-stability.