<< View SCS Blog
Protecting Solar Panel Electronics with Parylene
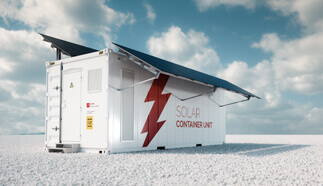
As with all renewable energy technologies, electronics play a crucial role in the operation of solar (photovoltaic) panels by facilitating the transformation, transmission and monitoring of the system. Unfortunately, system electronics are often delicate, making them the weakest link in the panel setup. Harnessing the sun’s energy to generate electricity, solar panels have demonstrated their utility in numerous applications. At the core of these panels are the solar cells, capable of energizing small devices such as calculators, rechargeable batteries, and watches. On a larger scale, complete panels can be tailored for broader functions like powering residences, lighting systems, and water treatment facilities.
While photovoltaic solar panels serve as efficient generators of clean energy, prolonged direct exposure to the sun and harsh elements can lead to their degradation over time. Utilizing appropriate material structures is crucial to shield solar panels from such extensive exposure, thereby enhancing their operational reliability and lifespan.
Parylene Conformal Protection for Solar Panel Electronics
Of existing conformal coatings, Parylene provides optimal protection and performance assurance for solar panels. Its chemical vapor deposition (CVD) application process enacts molecule-by-molecule penetration of substrate surfaces. Tiny coating particles adhere to every surface, penetrating every crevice and corner of the substrate, resulting in a truly conformal coating of the solar assembly. Protection of panel electronics surpasses the brush/dip/spray methodologies of liquid coatings such as acrylic, epoxy, silicone and urethane. Parylene offers the best overall panel security and performance benefits of all the conformal coating types.
Parylene conformal films offer a range of functional benefits, including:
- Chemically inert, solvent resistant panel substrate defense
- Consistent performance reliability
- Dry lubricant film properties
- Excellent resistance to incursions of moisture, salt sprays/mist
- Plasticity sufficient for use with flexible and semi-rigid circuits with a low incidence of surface cracking
- High tensile strength
- Negligible, stress-free surface tension to provide superior protection for densely populated substrates and the most intricately designed solar circuits, whether flex-designed or rigid,
- Optical transparency
- Particle immobilization
- Pinhole-free coating uniformity
- Thermal stability
- Ultra-thin, light weight with low outgassing
- Very high dielectric properties
These properties are very well aligned with conformal requirements for solar panel electronics, which include a need for:
- Flexibility: The capacity to be sufficiently supple to accommodate positional changes in the cell’s substrate, maintaining function without the formation of cracks to the film and subsequent delamination.
- Hermetical dependability: Completely sealing the panel’s electronic assemblies, protecting it from chlorofluorocarbons, H2O, O2 and similar agents of product degradation found in the external environment,
- Minimal gas permeability: The conformal barrier should obstruct potential penetration by gases such as oxygen and moisture.
- Stability: Parylene offers the necessary anti-corrosive, chemical, dimensional, electrical, and thermal stability to maintain solar panels’ functionality.
- Processing flexibility: Coating compatibility with solar assembly supports economic and energy minimization during the panel’s operation.
Solar panel/module systems typically come with a warranty spanning 25-30 years. Premium solar panels incorporate high-quality electronic components and precision electronics to ensure consistent energy output. However, despite their dependability, these panels can succumb to wear and tear in demanding conditions. Unfortunately, the majority of panel electronics require replacement within 10-15 years, which is less than half of the panel’s intended lifespan. This often leads to increased downtime and repair costs.
Parylene’s exceptional barrier properties offer dependable protection for solar farms near the ocean or seaside. It boasts minimal outgassing, rendering it resilient against saltwater and harsh winds, ensuring optimal panel performance. In contrast, liquid conformal coatings suffer damage under such conditions, leading to a significant decline in transmission signals and overall farm efficiency. Moreover, Parylene protective films are minimally affected by altitude changes.
Conclusion
Solar devices often rely on Parylene conformal coatings for crucial applications. These coatings play a key role in extending the operational life and enhancing the performance quality of solar panels, thereby promoting their wider adoption for energy generation. By leveraging Parylene’s functional attributes, solar devices benefit from enhanced protection of panel electronics across various operational conditions. The use of Parylene films effectively mitigates degradation and other failure mechanisms that can hamper solar panel performance, resulting in prolonged operational lifespan and increased efficiency in producing clean solar energy.