<< View SCS Blog
Parylene: The Military-Grade Conformal Coating
Military and defense equipment are put to the test and subjected to uniquely harsh conditions on a daily basis. These mission-critical products must be rugged and able to withstand extreme temperatures and weather conditions, exposed forces of gravity that are well above and beyond normal situations and a range of contaminants such as salt, water and fungus. Luckily, using Parylene conformal coating to protect electronics can ensure that components are fit for duty in the military and defense industries.
Conformal Coatings: To Protect and Serve
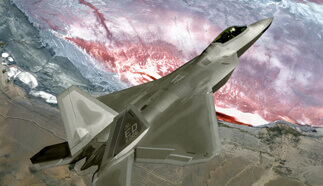
A conformal coating encapsulates electronic printed circuit boards (PCBs) and other critical components to protect them from such factors as outside elements, physical damage and hazardous chemicals. Conformal coatings also boast good dielectric properties; they protect the coated component from outside interference and signals, but also help to insulate the parts on the PCB and the etched traces from each other. This ultimately allows for a smaller board.
Parylene’s Unique Benefits
Conformal coatings can be made from a range of different compounds, but none has the unique benefits of Parylene. Parylene is deposited as a vapor at room temperature, protecting temperature- and chemical-sensitive components from damage during the coating and curing process. It can withstand extreme temperatures. Parylene is also hydrophobic and can withstand a 144-hour salt spray test, which exceeds the MIL-STD-810F ruggedization standard.
In addition to its strength, Parylene is both ultra-lightweight and very thin. It can completely permeate a space as small as 0.01 mm. The conformal coating is also pinhole-free at 0.5 microns. In military applications, where controlling component size and weight are important considerations, Parylene is the most-efficient conformal coating material available.
Military Coating Applications
Military electronics are frequently protected by conformal coatings. These coatings are so effective that, in many cases, they make commercial off-the-shelf (COTS) components safe for use in military settings. Some applications include:
- Portable radio sets. Military radio electronics need to be extremely rugged to survive battlefield use. But at the same time, they contain sensitive digital electronics. Parylene conformal coatings protect PCBs without adding additional weight or size, keeping products as compact and lightweight as possible. Their dielectric properties also help to prevent interference and crosstalk.
- Vehicle electronics. The electronic systems in military ground vehicles are frequently protected from moisture, chemicals, vibration and dust by the application of Parylene conformal coating.
- Aircraft lighting. As more military planes use LEDs as an efficient and long-lasting light source, they’re faced with the challenge of moisture ingress. Parylene conformal coating, applied as a gas, gets into and around tight geometries to encapsulate the assembly and ensure reliability.
- Exposed surfaces. Optical glass, radiation sensors and radar transmitters all benefit from the use of a Parylene conformal coating to protect them from the elements. Parylene’s exceptional coverage and low permeability make the conformal coating an effective protector of exposed surfaces.