<< View SCS Blog
Parylene for Defense Applications
What is Parylene?
Parylene is a conformal protective polymer used for coating, first postulated by Michael Szwarc in 1947. His early experiments involved the decomposition of the solvent p-xylene. His worked proved that when the vapors of the p-xylene reacted with iodine, para-xylyene di-iodide was the only resulting product. The reaction produced only a low yield and the process was later made more efficient by William F. Gorham.
Today, Parylene coating is used to uniformly protect any component configuration. Its unique features allow it to be used effectively on a diverse range of materials, including metal, ceramic, paper, plastic, ferrite, resin and silicon. It can be made to conform to any shape, including sharp edges, crevices, points, flat and exposed internal surfaces. Parylene works under pressures, stresses and in environments that would be detrimental to other types of coatings.
What are Main Uses of Parylene within a Defense Context?
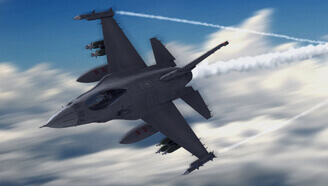
The main purpose of a conformal coating is to encapsulate critical components and protect them from external hazards such as harsh weather conditions, chemicals and physical damage. The versatile nature of Parylene means that it has a wide range of uses within the defense industry. It can be used on components that are put under constant extremes and are contact with changing contaminants. It also has dielectric properties that allow it to protect against signal interference. Paryene’s ability to do this while being both lightweight and ultra-thin means that it does not add to the overall size and weight of the circuit board.
Circuit boards and Hybrid Circuits
Parylene is thinner than other forms of protective coating. It’s also stress free and highly resistant to attack from fungi and solvents. The excellent adhesion of Parylene to ceramic substrates aids in minimizing the ionic conduction at the coating-substrate interface. Parylene coating also strengthens solder joints, which in turn strengthens the circuit links and wire bonds, increasing the lifespan of the circuit and its components. Parylene’s low dielectric constant also minimizes loading in high frequency applications.
Parylene coating can be deposited in exceptionally small spaces and has been used within spaces as narrow as 10µ. Due to its nature, Parylene can also be used to coat interior elements through a hole of just 1mm. Using Parylene coating also causes the termination of movement in particles such as balls of solder, left over from the manufacturing process.
Components
The reduction of friction is a key concern in manufacturing equipment and technologies for the defense industry. Minimal friction is essential to ensuring smooth operations and minimizing overheating and fire risks.
Elements such as ferrite cores and bobbins require coating to reduce friction. Parylene is highly effective at reducing friction and minimizing abrasion during coil forming. It has the additional benefit of preventing the formation of dust on components and protecting them from chipping. Parylene coating also provides electrical insulation and protection against corrosion to cast metal magnets. It is an ideal coating system for components such as accelerometers, strain gauges and pressure sensors that require environmental protection.Rubber and Plastic
Defense equipment needs to work effectively in any situation and under a variety of extreme conditions. It needs to be able to come into contact with chemicals and solvents without compromising the equipment. Parylene coating protects even the smallest elements.
The Parylene coating process allows it to penetrate the surface of rubber and plastic components. Adhesion is exceptional and gives a surface covering that is free of air bubbles, which minimizes opportunities for the external environment to compromise the component. A 2µ coating creates wear resistance and applies dry lubricant feel and appearance to the surface. Chemical and solvent resistance can be increased by using a thicker coating.
How is Parylene Coating Engineered and Tested?
Engineering Parylene coating is an intricate multistage process. Many aspects of the process are specific to the coated material. These include the Parylene variant, thickness of the coating and the time taken to apply the coating effectively. The process begins before the materials have even been received.
Stage One: Information Collection
Before the coating can be applied, as much information as possible is gathered about the item that is to be coated. This information will come in the form of written descriptions and drawing and include:
- Dimensions of item
- Composition of the item
- The stresses/environment it is likely to be subjected to
- Coating free areas
- Specific customer requirements
Stage Two: Inspection
The item to be coated is carefully inspected for any damage. The inspection team will also ensure that it meets the specifications that have been previously discussed. A rinsing process will also be undertaken at this time if required.
Stage Three: Masking/Prep
Once inspection and rinsing, if necessary, has been completed, the item will be masked in accordance with the customers’ specifications, ensuring that the coating is only applied in the requested areas. Any surface preparation is also completed during this stage.
Stage Four: Coating
The item is now ready to be coated. The solid-state raw material, called dimer, is placed in a loading boat, which is then inserted into a vaporizer. The variant of raw dimer will be dependent on the item being coated (the main variants are C, D, N and Parylene HT®). The dimer is heated to a minimum of 100°C (212°F) and the vapor pulled through vacuum into a furnace. Here it is heated to a higher temperature, allowing the molecules to be split and the monomer to be created. The monomer, still in gas form, continues to be pulled through the vacuum in single molecules onto the item. This is done in the coating chamber at ambient temperature, and the gas molecules polymerize evenly on all substrates, forming Parylene coating on customer parts.
Stage Five: Post Coating
Once the coating process is completed, the masking is removed. This needs to be done with extreme care so that the newly applied, ultra-thin coating is not damaged. This is followed by a final inspection of the completed item, during which the item will be compared to the original customer request and specifications. After the item has passed the inspection, it is sent to the shipping department and returned to the customer. Close contact is kept with customers to ensure that the item or materials have met their needs and are working as expected.