<< View SCS Blog
Parylene Conformal Coating for Medical Use
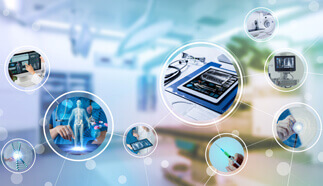
Parylene conformal coatings have protected medical device components with an extended range of applications for 50 years. They offer both patients and medical personnel a highly reliable level of uniform, biocompatible protection on components that range from the simple to the highly complex. Their value and application will continue to proliferate, as technology develops.
Organic Polymers used as Coatings
The overall generic name Parylene designates a unique set of organic polymeric coating materials with countless applications across all markets. All commercially applied Parylenes are polycrystalline and linear in their deposited configuration. The four variants commonly used in the medical market are Parylenes N, C, Parylene HT® and ParyFree®.
In general, Parylene materials possess properties similar to polytetrafluoroethylene (PTFE), better known as Teflon™. However, they have proven to outperform most competitive coatings, including Teflon, for most medical purposes and for other industrial/product uses.
Parylene is chemically inert, further adding to its safe use as a coating for medical equipment. For the same reasons, it poses minimal potential for infection or for causing altered data readings in the form of signal interference. The exceptional biocompatibility of Parylene fits nicely into the development and implementation of today’s most advanced devices, including minimally-invasive implant technologies and surgical tools. Parylene’s barrier properties provide unmatched moisture and chemical protection, while generating a unique, dry lubricious surface. Its electrical properties insulate medical devices such as electro-surgical tools and cardiac implants.
Parylene has no negative impact on bodily functions, and has been used to enhance the body’s acceptance by presenting a benign surface. This beneficial quality has been demonstrated by its hemo-compatibility and minimal fibrous capsule formation; nonexistent toxicological responses have been recorded in virtually all cases of use.
With these characteristics, Parylene conformal coatings are adaptable for many product uses and possess superb qualities for medical device applications.
Medical Product Applications of Parylene
Biocompatible, Parylene conformal coatings protect medical devices from chemicals, fluids and stray electrical charges. Parylene ensures:
- Patients are not infected by a device implanted within the body
- Protection from contamination by bodily fluids and functions, so the device continues to perform and function as expected.
Durable Biocompatibility
Parylene’s physical properties play an important role in its medical uses. Applied through a vapor deposition process, the coating retains compositional stability and performance in the presence of body fluids and tissues. While many other substances can generate similar characteristics, Parylene is unique in providing one of the thinnest effective coating applications available. Thus, surfaces coated with Parylene can be safely situated in less accessible, more-constricted regions of the body than those otherwise coated. The ultra-thin film adds minimal mass to delicate medical components, while retaining the highest levels of protection during use. Low dissipation factors can mean extended product performance and longer-lasting functionality; the result is not only enhanced treatment-performance, but safer use for more functions in critical, difficult-to-reach regions of the body. Parylene coated devices also are suitable for medical application because they withstand most common sterilization methods. These factors combine security with durable biocompatible service.
Superior Medical Product Service
Parylene coatings are noted for their exceptional crevice penetration of surfaces to be protected. Therefore, surface pinholes that lead to leakage are eliminated because Parylene conforms precisely to substrate contours. While protecting the exterior of components and devices, Parylene also generates excellent dry-film lubricity, often enhancing device performance and medical care, as well as reducing patient discomfort.
Recommended Parylene Products
Parylene coatings have long provided surface protection for such traditional medical devices as hypodermic needles and syringes, catheters, cannulae, medical bottles, and hearing aids. Over time, they were effectively applied to coronary stents, and medical probes, electrodes, and circuits/printed circuit boards (PCBs) for medical devices.
Electrosurgical (ESU) and powered surgical (PSU) devices as well as pneumatically-powered surgical instruments feature Parylene protected surfaces. The dielectric properties of Parylene are often the key enabling technology for implementation.
Parylene applications for microelectromechanical systems (MEMS) implantables have also grown significantly for a wide range of devices. These include non-coiled guide wires, pacemakers, defibrillators, heart-lung bypass pumps or intra-aortic balloon pumps. Sensors for diagnostic monitoring of patients’ conditions represent just one product area that requires the use of advanced surface modifications, including high performance conformal coatings.
ISO 10993 biological evaluations of Parylene coated medical devices have found them imminently safe for use in all the cases above. These applications provide only a few examples of a growing list of efficient Parylene-based or assisted medical applications.
The use of Parylene on critical medical devices and components continues to grow by virtue of its unique set of performance attributes. The barrier properties, electrical insulation and dry film lubricity of the Parylenes will continue to benefit future advancements in patient care, often without even making themselves known to the end user.