<< View SCS Blog
Parylene and Hydrofluoric Acid
Parylene is a chemically inert conformal coating [1]. It has a well-established vapor deposition process and patterning methods. It is a great candidate for use in various application areas (health, aerospace, oil and gas, microelectronics and so on.) due to its mechanical, physical, optical and chemical properties. Parylene is known to withstand highly corrosive environments, and it can be utilized as a barrier material against various etchants in different processes (e.g. Hydrofluoric acid (HF), nitric acid, acetic acid, potassium hydroxide, and tetramethyl ammonium hydroxide). Spin/spray-coatable or brushable polymers such as epoxies and urethanes have been proposed and used to protect against hydrofluoric acid. However, Parylene can be conformally coated on all kinds of geometric shapes with precisely controlled thicknesses, providing superior protection. Therefore, it is an attractive protective conformal coating layer compared to all the other proposed methods.
There is no known or reported chemical reaction between Parylene and common etchants such as hydrofluoric acid, and one can assume that Parylene will not be damaged during etching processes. Several experiments have confirmed this claim [2].
Most research focuses on answering the following questions:
- How thick should Parylene be to provide decent protection?
- What is the etching selectivity with respect to the targeted material to be etched in hydrofluoric acid?
As an example, corrosion of surface oxide of polysilicon wafers takes place in the hydrofluoric acid at any concentration, which leads to the change in the surface morphology of the wafer and device failure due to the detachment of electrodes from the electronic devices. Also, buffered hydrofluoric acid (BHF) is used to remove surface oxide of electrodes to improve the contacts (aluminum oxide, copper oxide, titanium oxide, etc.) to enable its use a good protection for the rest of the product is essential. Parylene protective coatings can prevent the corrosion of masked parts in such cases.
The thickness of the Parylene plays an important role because it is also prone to swelling at lower thicknesses. In a study on the Parylene protection of surface micromachined polysilicon film, it was shown that a Parylene conformal coating of 0.5–2 μm can withstand 40 min exposure to 40% HF (Fig 1)[2]. In the study, Parylene type C was coated and patterned using an O2 plasma system, with an A174 adhesion promoter applied before the deposition process. 40% HF is a very high concentration level and 40 minutes exposure is a relatively long time for such processes. As a conclusion, the thicker Parylene is, the better etch-masking ability it provides. Some studies suggest a high temperature annealing, 350°C, for several hours, under vacuum or in an inert environment of Parylene conformal coating to improve its stability in hydrofluoric acid as well [1].
Figure 1: SEM of Al with 2 μm parylene after 40 min HF etching.
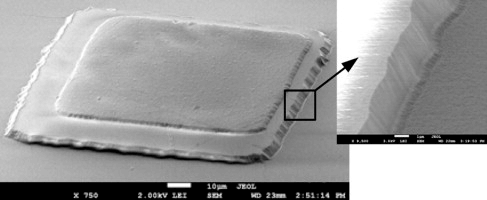
A different group of researchers has shown that Parylene is a decent masking material for use in HF vapor release for MEMS/NEMS systems [3]. A thick layer of Parylene is sufficient for use in liquid HF or gaseous HF. Lower thickness Parylene/Al/Parylene stack is suggested as a protective coating as well [3].
In conclusion, Parylene does not react with hydrofluoric acid and is safe to be used as a protective masking layer (encapsulation) when applicable.
References
[1] Hsi-wen Lo, Wen-Cheng Kuo, Yao-Joe Yang, and Yu-Chong Tai, “Recrystallized parylene as a mask for silicon chemical etching,” in 2008 3rd IEEE International Conference on Nano/Micro Engineered and Molecular Systems, Sanya, China, 2008, pp. 881–884, doi: 10.1109/NEMS.2008.4484464.
[2] Y. Zhang, Y. Wang, M. Cai, Y. Wang, Y. Hao, and J. Chen, “Metallization introduced corrosion and parylene protection of surface micromachined polysilicon film with submicron capacitive gap,” Microelectron. Eng., vol. 97, pp. 20–25, Sep. 2012, doi: 10.1016/j.mee.2012.03.010.
[3] A. Higo, K. Takahashi, H. Fujita, Y. Nakano, and H. Toshiyoshi, “A novel Parylene/Al/Parylene sandwich protection mask for HF Vapor release for micro electro mechanical systems,” in TRANSDUCERS 2009 – 2009 International Solid-State Sensors, Actuators and Microsystems Conference, Jun. 2009, pp. 196–199, doi: 10.1109/SENSOR.2009.5285531.