<< View SCS Blog
The Impact of Temperature on Parylene Adhesion
Basic Thermal Properties of Parylene Conformal Coatings
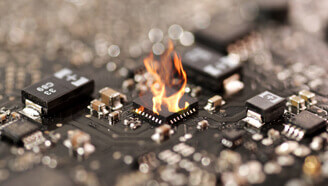
Vapor deposited Parylene combines high thermal stability with a low dielectric constant, minimal moisture absorption and other advantageous properties which sustain its adhesion to substrate surfaces. Among the most beneficial of Parylenes’ thermal properties is their ability to function at an exceptional range of temperatures. Depending on the Parylene type, they are operative at temperatures as low as -271ºC, and as high as 450ºC, representing an ability to perform within a span of 721ºC.
Coating performance depends upon the specific Parylene type, its explicit product purpose and the environmental use conditions. When Parylene type and purpose are appropriately matched to the expected thermal conditions of the assembly’s operational environment, Parylene conformal coatings offer superior adhesion and performance.
As an example, Parylene C can endure constant exposure to 100°C for 11+ years in the presence of oxygen, accounting for 100,000 hours of use without appreciable delamination. In contrast, more recently developed Parylene HT® is useful in high temperature applications (continuous use at 350°C and up to one hour at 450°C), although this represents an extreme range. Generally, Parylenes can provide similar service (11.4 years) in vacuum, or atmospheres free of oxygen, with continuous exposure to 220°C, making them an excellent choice as conformal coatings for aeronautics and space flight uses.
Further thermal properties of commercially available Parylene types are provided in Table 1.
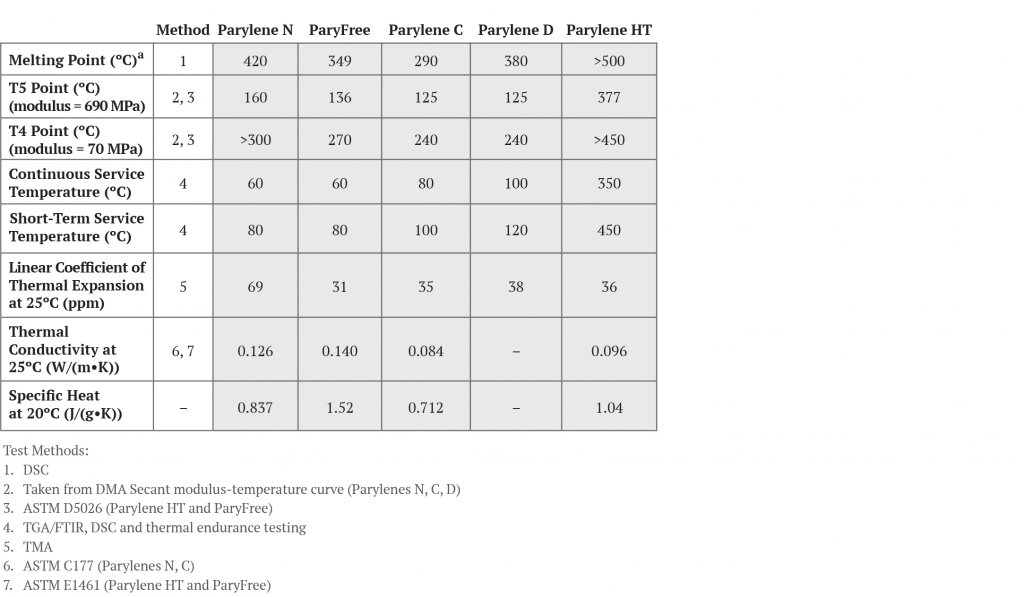
Optional Methods to Improve Parylene Adhesion
Optimal adhesion of Parylene to a wide variety of substrates is commonly achieved by a treatment with A-174 silane prior to Parylene coating. Sometimes, however, it fails to meet the highest standards on many of today’s difficult substrates (e.g., highly polished stainless steel, titanium, exotic alloys and polyimides, etc.). SCS’ AdPro family of technologies increase adhesion between Parylene coatings and historically challenging substrates and has demonstrated stability at elevated temperatures, making this adhesion-enhancing option an excellent choice for high value applications.
While not common, Parylene may be annealed under vacuum to increase cut-through resistance, enhance coating hardness and improve abrasion resistance. This is the result of a density and crystallinity increase. At the same time, properties of crystallinity and surface morphology generally undergo some degree of transformation during deposition and thermal annealing, affecting Parylene film adhesion as well. These conditions suggest that when faced with unique and/or extreme conditions, proper treatment can result in improved coating properties and adhesion, i.e. the incidence of failure due to film delamination can be limited if processes are carefully and thoroughly implemented.
Despite rare inconsistencies of performance under conditions of thermal stress, Parylene’s properties generally provide very good thermal adhesion and endurance for innumerable products and purposes, particularly when compared to competing coating materials. In extreme cases of terrestrial application, higher operating temperatures may shorten Parylene’s functional life. Oxygen-free, space environments (the vacuum of space) do not affect the Parylenes, which can operate for extreme durations at higher temperatures (220°C+). Testing the coated, finished assembly under conditions closely resembling intended operating settings is recommended to verify its ability to withstand or exceed these temperature-time-atmospheric conditions.
Parylene reliably performs under a wide range of situations – in air or a vacuum – at a wider temperature range than competing conformal coatings. It does so for a decade or more, at an extreme range of temperatures, without significant loss of physical properties, providing superior adhesion and limited delamination.