<< View SCS Blog
Is Conformal Coating Necessary for PCBs?
When designing a product or system, the PCB is one of the most critical components, supporting main functions like power supply and communication. It is key to maximize the PCB’s working life and protect it from harsh environments. Conformal coating provides PCBs the protection needed to endure various conditions and work reliably. Utilizing conformal coating for PCBs comes with many advantages, while not using it carries many risks.
What Is Conformal Coating?
Conformal coating is a kind of thin polymeric film. This film is applied to a PCB and conforms to the PCB’s contours. Since conformal coatings provide a non-conductive and defensive dielectric layer, they are commonly used to protect various technologies. Coatings can be found on uncovered traces, electronic components’ leads, solder joints and other metallized sections of an electronic device or PCB. Generally, the film is applied at 10-150 µm.
When applied correctly, the film protects electronic equipment and PCBs from corrosion and dangerous environmental factors, such as mildew, salt spray and moisture. The film also prevents electromigration and dendritic growth. As a result of the increased protection conformal coating provides, its usage helps extend the life span of PCBs.
How Does Conformal Coating Work?
Conformal coatings are placed on top of sensitive electronic parts that could be harmed by environmental conditions. Once applied, the coating essentially creates a defensive wall between the electronic parts and dangerous materials, such as debris, chemicals and moisture. Conformal coatings will not act as a total sealant. Instead, they provide a breathable protective layer, allowing any dampness trapped in the circuit board to dissipate.
Specific Conformal Coating Types for PCBs
Numerous conformal coating types are used to protect PCBs. Each coating type offers various benefits and drawbacks. Discover the key types of conformal coatings for PCBs below.
- Acrylic coating: Acrylic coating tends to be solvent-based with moisture-proof and anti-fungal properties. This coating is often characterized by its transparency, durability and hardness. Acrylic also tends to be easily repairable due to how soluble it is in many kinds of organic solvents. It’s well-known for its fast drying properties and relatively long service life. Though it offers lots of advantages, it doesn’t provide much stress relief for PCBs.
- Parylene coating: As a polymer-based compound, Parylene coating consists of crystalline and linear polymers and is known for providing strong moisture, chemical and dielectric barrier properties. The coating is transparent and can cover areas as narrow as 0.01 millimeters. The coating also features solid heat resistance and has a temperature range between minus 200°C to 350°C .
- Urethane coating: Urethane coating is a high-strength hard coating that provides high solvent resistance. It also has impressive dielectric properties and chemical resistance. Additionally, polyurethane coating tends to feature low moisture permeability, low-temperature adaptability and strong abrasion resistance. This coating type has some limitations, as it usually cannot be repaired and does not perform well in high-temperature environments.
- Epoxy coating: Epoxy coating is opaque and hard, excelling at resisting the negative effects of solvents and moisture. It’s easy to use and has a two-part thermoset mixture. Many people use epoxy coatings for chemical, moisture and abrasion resistance. Since the thermoset mixture shrinks during curing, it’s very difficult to remove the coating or repair the film without harming the PCB. Additionally, at extreme temperatures, the coating can put pressure on the PCB’s parts.
- Silicone coating: Silicone resin coating is very transparent and soft, providing PCBs with good moisture, chemical and corrosion resistance. The coating has a similar moisture resistance to acrylic and urethane, as well as good thermal shock resistance. It also works well at high temperatures and features light transmission properties. One drawback to this film is that it does not have high dielectric resistance compared to other coatings.
Why Should I Use Conformal Coating for PCBs?
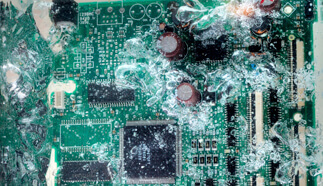
Conformal coating is essential to protect PCBs from contaminants and dangerous environments. For instance, excess moisture can speed up decomposition, reduce insulation resistance and result in conductor corrosion. Contaminants can also cause unrecoverable shortcuts, corroded conductors and electrical failures. Essentially, conformal coating provides PCBs with the protection they need to operate at a high level.
Conformal coating benefits for PCBs include:
- Improved product design robustness: One of the biggest draws to using conformal coating is its ability to protect PCBs from harsh environments, including extreme temperatures, moisture, smoke, dust, residues, sand, acids and other contaminants.
- Extreme thinness: Circuit boards and devices often have thickness and weight restrictions. A clunky protective film simply is not an option. A major advantage of using conformal coating is that it is thin enough to be applied on devices and PCBs with the tight space restrictions.
- Reduced maintenance and replacement costs: Since conformal coatings protect PCBs, they reduce the damage PCBs sustain, resulting in the reduced maintenance or replacement. Lowering the possibility of damage saves money and time.
- Multiple coating processes: Coatings can be applied by many application methods, including brushing, spraying, or vapor deposition.
- Improved inspection: Conformal coatings can include ultraviolet (UV) tracers. These tracers make it easy to inspect the coating with an ultraviolet light source. You can use the light to ensure the coating does not have any cracks, foreign matter, air bubbles or flaking.
Do PCBs Need Conformal Coating?
It’s almost always necessary to use conformal coating for PCBs to ensure key electronics run at peak efficiency and offers reliability in essential applications. The consumer electronics, automotive, military, energy system, industry control and medical industries rely on coatings to protect numerous devices.
Risks of Not Using Conformal Coating for PCBs
Conformal coatings increase functionality, provide protection and prevent failures. The reliability of a PCB is at risk if it is not protected by a conformal coating and could result in costly failures. While conformal coating comes with some costs, it adds value and can offset the expenses associated with repairs and failures. Risks include:
- High repair costs: When a PCB fails prematurely, the materials and labor required to fix it are costly. Without the protection of a conformal coating, it is likely repair will need to be made more often, leading to higher costs.
- More replacement expenses: Much like maintenance costs, replacing damaged PCBs can be expensive. Coating PCBs reduces the chances of having to replace a PCB prematurely.
- Damaged reputation: When products or equipment do not work as intended, a company’s reputation is at risk and customers may turn to another vendor. Ensuring the reliability of PCBs with conformal coating offsets this risk.