<< View SCS Blog
IoT (Internet of Things) & Parylene Conformal Coatings
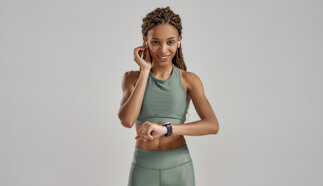
The Internet of Things (IoT) enables us to link everyday objects to the internet. It comprises a network of interconnected devices, vehicles, appliances, and various other items. IoT functions through the integration of sensors, actuators, electronics and embedded software. Data gathered from these physical devices are exchanged via network connections to enhance operational efficiency. This technology finds diverse applications in defense, security, healthcare and industrial sectors. Wearable gadgets, underwater systems, agricultural innovations, smart home solutions, automotive advancements, aviation systems and various other domains benefit from the utilization of IoT devices.
Smart home technology has undergone significant advancements in recent years, facilitating seamless connectivity for smart doorbells such as Ring, integrated screens by Amazon and wearable/hearable devices that enhance our interconnectivity with other devices.
The Role of Sensors in the Internet of Things
IoT devices contain sensors that can detect the position, acceleration, pressure, temperature, humidity, etc. Today, it is possible to design and manufacture IoT devices that are lightweight, multifunctional, reliable and efficient. Reliability hinges on their ability to deliver consistent long-term performance across diverse environments.
How to Protect Your IoT Devices
Highly diverse applications and environments necessitate meticulous maintenance and protection of electronic components, power systems, and signals from environmental factors. While specialized plastic casings exist, they often compromise the compactness and lightweight design of IoT devices. Various manufacturers offer custom-made PCBs tailored for specific applications.
Parylene thin films offer pin-hole and stress free complete coverage. They can be used under almost any environmental condition provided that the right Parylene variant is used. Parylenes are all colorless and they are aesthetically pleasant. Their mechanical strength and high breakdown voltage make them attractive as protective coatings. They exhibit high dielectric strength which makes them favorable as insulators and the dielectric properties can be tuned by modifying their thickness. Parylene protective coatings can withstand cryogenic and relatively high temperatures (-400°F (-200°C) to +662°F (+350°C)) while maintaining their electrical and mechanical properties which is a rare property in materials systems. These properties collectively position them as ideal for serving as a protective coating in IoT applications.
Parylenes C and N and Parylene HT® are all used in microelectronics and PCB applications. Among them, Parylene C stands out as the most prevalent choice, meeting FDA regulations for biomedical use, specifically ISO 10993 biological evaluation of medical devices regarding microfluidic devices and medical implants. This makes Parylene C suitable for use in medical IoT devices like implants and wearables, designed for skin contact in data collection processes (e.g. heartbeat, body temperature, sweat analysis, cochlear implants, etc.) [1].
Parylene HT stands out for its remarkably low dielectric constant of 2.17 @ 1 MHz, making it a coveted choice for conformal coating due to its immunity to photo degradation and wide thermal stability range. Notably, Parylene HT boasts a high melting point (≤ 500°C), surpassing that of Parylene N (420°C) and Parylene C (290 °C).
Parylene N, on the other hand, is preferred for applications requiring a consistent dielectric coefficient across all frequencies, offering a more cost-effective alternative.
Flexible and lightweight sensors for IoT: Parylene as a conformal coating

Examples of sensors and systems constructed using flexible Parylene layers can be found in both academic literature and industry publications. Flexible and 8 μm thick micro temperature and humidity sensors on Parylene thin films were reported by Chi-Yuan Lee et al in 2008 as shown in the image below[2]. These flexible sensors offer light-weight and highly reliable systems to be used under compression. The sensitivities of temperature sensor was reported as 4.81 × 10−3 °C−1 and humidity 0.03 pF/%RH.
Hong Lei et al reported the production of Ionic polymer-metal composites (IPMCs) with thick (up to 25 micrometers) Parylene C coating. Their motivation was the inconsistent sensing properties of IPMCs when operating in air under different humidity levels, or after exposure to different ambient media. After developing an effective coating processes, and evaluating the performance of the Parylene C encapsulated sensors they reported that the conformal coating can isolate the IPMC sensor from various ambient environments and maintain the functional consistency of the sensor [3]. Similar results were reported by Seong Jun Kim using Parylene with IPMC sensors in an earlier study [4].

Implantable micromechanical Parylene-based pressure sensors for unpowered intraocular pressure sensing were demonstrated by Po-Jui Chen et al. They monitored the pressure response of the implant with the goal of realizing convenient, direct and faithful IOP monitoring in glaucoma patients. They showed the biocompatibility and functionality of the implant fixation method inside the eye as well. [5].
In summary, Parylene stands out as a dependable, safe, lightweight and adaptable material suitable for serving as a flexible packaging solution or a protective conformal coating for electronic components on PCBs or other electronic devices.