<< View SCS Blog
How to Choose the Best Conformal Coating for Your PCB
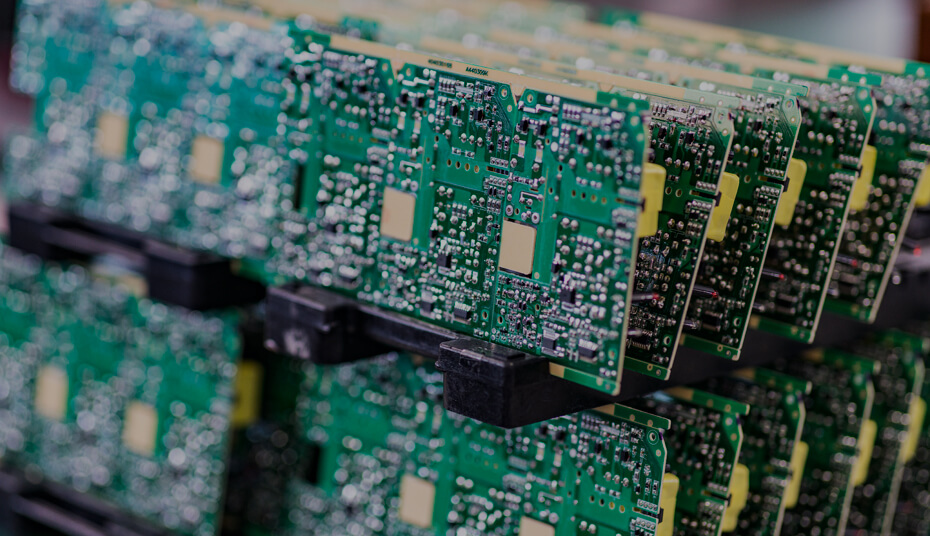
Printed circuit boards (PCBs) are the foundational building blocks of almost all modern electronic devices. They can be found almost anywhere, including in smartphones, cars, planes and in many other common applications. Because PCBs are essential to the operation of many electronic devices, they must be protected from any and all elements that could alter their functionality. Many PCBs rely on conformal coatings to provide the high level of protection they need.
This article will walk through how PCBs can be protected with conformal coating, the different types of conformal coatings and how to choose the best conformal coating for a PCB.
What is Conformal Coating for PCBs?
A conformal coating is a thin polymeric film applied to a PCB to protect the board and its components from the environment and corrosion. The film completely conforms to the shape of the PCB to protect all of the solder joints, leads of electronic components, exposed traces and any other areas that are vulnerable to corrosion.
Why do you need conformal coating? When a conformal coating is applied to a PCB, it extends and enhances its working life. Applying a conformal coating can allow for higher voltage gradients and closer track spacing, which enables designers to meet and exceed standards. It is important that electronics are adequately protected from external elements that can cause device failure and lead to serious consequences. These elements may include moisture, salt spray, chemical exposure, temperature extremes, etc.
Types of Conformal Coating for PCBs and Their Pros and Cons
There are several types of conformal coatings available with different sets of properties and characteristics. Each coating type has varying strengths and weaknesses that should be considered when making your PCB coating selection.
Acrylic (AR)
Acrylic conformal coatings are the most popular type due to their ease of application and removal and their forgiving nature.
Pros
- Easily applied/removed
- Easy rework and repairs
- No shrinkage during the curing process
- Affordable
Cons
- Low chemical and solvent resistance
- Low abrasion resistance
- Struggles in harsh environments
- Not ideal for high-temperature applications
Epoxy Resin (ER)
Epoxy conformal coatings are typically available as a two-part compound that begins curing upon mixing. Single part coatings can be cured thermally or with UV exposure.
Pros
- Abrasion and moisture resistance
- Great chemical resistance
- Good humidity resistance
- Durability in harsh environments
Cons
- Hard to remove
- Shrinks during the curing process
- Soldering iron required for rework or repair
Silicone Resin (SR)
Silicone resin conformal coatings are single-component compounds that are typically applied to electronics that will be used in extreme temperature ranges.
Pros
- Good in extreme temperatures
- Excellent humidity and corrosion resistance
- Good chemical resistance
- Adheres to most PCB components/materials
Cons
- Very difficult to remove
- Requires strong chemical strippers and harsh abrasion for removal
- Localized repairs only
Parylene (XY)
Parylene conformal coatings are applied in a vapor deposition process. Because the coating is applied as a gas, Parylene penetrates crevices and under components, providing ultra-thin, perfectly conformal protection.
Pros
- Best solvent and extreme temperature resistance
- Transparent and colorless
- Applied at room temperature and does not require curing time
- High dielectric strength
Cons
- Hard to remove and must be abraded off
- Not ideal for long-term outdoor exposure
- Special equipment needed for application
Considerations for Selecting PCB Conformal Coating Material
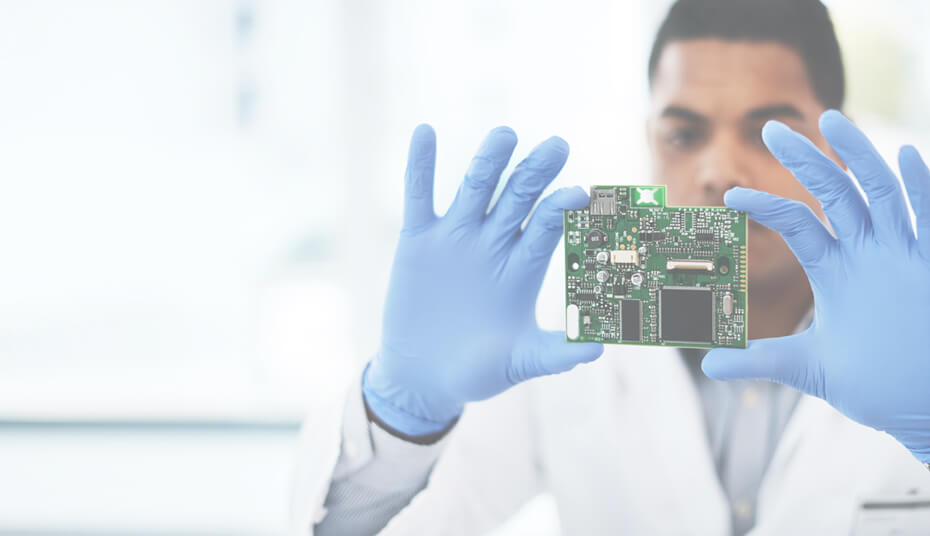
What is the best conformal coating for your PCBs? With numerous conformal coating types available, it is important to find the one that will withstand the challenges your PCB will face and best aligns with your needs. The top three factors to consider when selecting a conformal coating are product use, temperature range and environmental factors.
Product Use
The most critical factor to take into consideration is the intended use of your product. It is key to compare the pros and cons of each of the different coating types based on the product end use.
For example, a PCB going into a product that will be exposed to water needs protection against extreme moisture exposure. Based on the characteristics of all the conformal coatings, Parylene conformal coating may be the best option. Parylene is known for its moisture protection, including IPX7 and IPX8 waterproof protection.
Temperature Range
When determining the type of coating for your product, you should have a clear understanding of the minimum and maximum temperatures it will be exposed to. Temperature ranges are an extremely important factor to take into account. If a PCB is not coated to withstand the appropriate temperature range, it can result in damage to the PCB or failure.
For example, temperature extremes are an essential consideration for PCBs used in aerospace applications. Aircraft can see extreme temperature ranging from -65°C (-85°F) in the air to over 100°C (212°F) on the runway. Silicone is the only conformal coating that can handle extended use at this range.
Environmental Factors
There are numerous environmental factors that can impact the performance of a PCB. Understanding what your product will be exposed to will help determine the best conformal coating for your PCBs. For example, the only environmental factors that would need taken into consideration in an application where a PCB is placed in a partially-sealed protective housing are condensation and humidity. Below are some other common environmental factors that should be considered:
- Extreme humidity
- Salt-spray environments
- Corrosive gasses
- Immersion environments
Specialty Coating Systems’ Conformal Coating Services
SCS provides multiple industry-leading conformal coatings and will work with you each step of the way to determine the best coating for your PCB. With 50 years of experience in engineering and applications, SCS is a world leader in conformal coating services and technologies. A direct descendant of the companies that originally developed Parylene, we leverage expertise on every project – from initial planning to process application.
Contact SCS today for more information on conformal coatings and how to select the best coating option to protect your PCBs.