<< View SCS Blog
Conformal Coating Selection: Weighing the Pros and Cons for Your Application
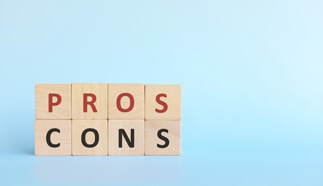
Utilized in medical device, electronics, defense, aerospace and transportation applications, conformal coatings are applied to a product to provide protection from hazardous substances and harsh environments. Optimal protection, however, is contingent upon proper selection of the conformal coating type. This critical task requires engineers to carefully weigh the benefits and drawbacks of the five main types of conformal coating, Parylene, acrylic, urethane, silicone, and epoxy—based on product needs.
Parylene
Many people consider Parylene to be the gold standard of conformal coating due to its plethora of desirable properties for applications ranging from printed-circuit boards (PCBs) to medical implants. Benefits of Parylene conformal coating is that it:
- Applied ultra-thin and pinhole-free at a coating thickness greater than 0.5 microns
- Features high optical clarity
- Offers excellent moisture and dielectric barrier properties
- Possesses desirable mechanical properties and dry-film lubricity
- Is chemically and biologically inert
- Adheres to a wide range of substrates and geometries
- Biocompatible and biostable
- Provides conformability and flexibility
- Penetrates extremely small spaces and crevices
- Contributes to tin whisker mitigation
- Withstands the heat of an autoclave
Drawbacks of Parylene conformal coating include:
- Higher costs compared to other conformal coatings, stemming from the cost of raw materials, labor and volume
- Requires an abrasion-based method for removal
- Has limited throughput
Acrylic
Acrylic resin is among the most common types of conformal coating. A typical application for acrylic resin—or type AR conformal coating—is providing moisture protection to PCBs. Acrylic’s primary advantages of acrylic resin is that it:
- Promotes ease of application via dipping, spraying, brushing, or robotics
- Enables easy coating removal for rework or repair
- Possesses advantageous moisture and dielectric barrier properties
- Dries rapidly and at room temperature
- Features low or no exotherm during cure
- Has a long pot life
- Resists fungus and humidity
- Does not shrink during cure
- Exhibits low glass transition (Tg) temperatures
- Represents a cost-effective conformal coating option
Acrylic resin conformal coating, however, may not be suitable for applications that require:
- High operating temperatures
- Exposure to moderate or strong solvents
- Coating hardness and durability
Urethane
Available in single- or dual-component, UV-curable, or water-based versions, urethane (type UR) conformal coating is often the optimal conformal coating choice for PCB protection and applications in which the product is exposed to chemical solvents. Urethane conformal coating:
- Retains high dielectric properties over sustained periods of time
- Provides humidity, abrasion and chemical resistance
- Protects substrates from moisture, harsh solvents and contaminants
- Offers durability, hardness and wear resistance
- Mitigates tin whisker growth
- Facilitates miniaturization because it insulates signal traces that are close together from one another
On the other hand, urethane conformal coating:
- Cures slowly
- Presents removal and rework challenges because of its solvent-resistant nature
- Cannot withstand high-vibration and high-heat environments
Silicone
Because of its ability to endure high-temperature environments, silicone conformal coating (type SR) is particularly suited for automotive applications. Among the benefits of silicone conformal coating is that it:
- Withstands prolonged exposure to high temperatures up to 200°C
- Exhibits stability across a wide temperature range
- Provides an excellent moisture barrier
- Offers high moisture, UV and corrosion resistance
- Features high dielectric strength
- Has low surface energy, which promotes enhanced wetting
- Promotes good adhesion to most PCB materials
- Cures rapidly
- Enables the application of thicker films, which provides thermal protection and vibration dampening
- Facilitates extreme ease of application and rework
Drawbacks to urethane conformal coatings include:
- Relatively poor wear and abrasion resistance
- Poor solvent resistance compared to other conformal coatings
- Requires more attention in order to achieve the optimal thickness
Epoxy
Offered as a single- or two-part compound, epoxy resin (type ER) conformal coating is defined by extreme hardness; however, that property is also its biggest drawback. Epoxy resin:
- Exhibits rugged toughness and durability
- Allows for ease of application
- Resists abrasion, humidity and chemicals
- Possesses good dielectric and moisture barrier properties
- Features relatively high glass transition (Tg) temperature
Like all conformal coating, epoxy resin has drawbacks as well. For example, epoxy coating:
- Presents significant challenges for removal and rework because of its toughness and durability, which puts the coated product at risk of being damaged
- Experiences shrinkage during polymerization
Selecting a conformal coating is a complex decision that is dependent on the application, volume and desired results. Each conformal coating offers a unique blend of benefits and drawbacks that must be considered in relation to a given application.