<< View SCS Blog
Conformal Coating for PCBs
Printed circuit boards (PCBs) electrically connect and power even the simplest electronic products. To function as designed, PCBs and their components – capacitors, resistors, etc. – require protection against operating problems caused by corrosive liquids, dust, physical shock and temperature extremes as well as the bodily fluids medical implants must endure. Conformal coatings are applied over PCBs to safeguard mechanisms and maintain functionality.
Selecting the optimal PCB coating depends on component type, board design, its operational environment, protection/weight requirements and the need for aftermarket modifications like repair or rework. These considerations are further modified by the differing properties of the five main conformal coatings available for PCB use.
Which Conformal Coatings are used for PCBs?
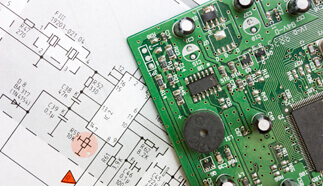
Conforming to PCB’s exposed physical configurations, coatings insulate assembly components, safeguarding specialized electronics’ functional integrity through extreme operating conditions.
There are five main coating types used to protect PCBs. The liquid coatings — acrylic, epoxy, silicone and urethane – represent the first four. Basic application methods for liquid coatings on printed circuit boards include brushing the wet coating material on to the substrate surface, immersing the PCB (dipping) in a liquid bath of coating substance and spray coating the PCB, either by manual application or through robotically-programmed treatment. While liquid methods can entirely cover a PCB, flashing and curing can leave surface defects like air bubbles or orange peel (irregular surface-levelling) that limit actual film protection. Irregular topography of the PCB surface can result in gaps in the coating, regardless of the liquid material used. Nevertheless, wet method films are frequently used because:
- Protection is generally efficient
- Ease of application
- Inexpensive
- Readily reworkable where defects exist
Chemically vapor-deposited (CVD) Parylene is the exception. Becoming a gas when heated, Parylene is directed through a vacuum chamber and polymerizes into a conformal film, effectively safeguarding PCBs. Because vaporous Parylene can penetrate every crevice of a substrate, regardless of topographical complexity, it is a truly conformal, pinhole-free coating. Drawbacks include cost and batch production capabilities.
Each coating material possesses specialized advantages and disadvantages as protective films for PCBs, which impact their use.
Selecting Coating for PCB Coverage
Selection of a reliable PCB-coating should analyze the response of each coating type to the unit’s electronic functionality and operational environment, for accurate assessment of the material’s adaptability to the PCB’s performance.
Acrylic liquid coatings are easily applied/removed/reworked and inexpensive; they do not shrink during curing and have high dielectric strength. However, both protective qualities and surface elasticity are limited compared to other coatings. In addition, their resistance to surface abrasion, chemicals and solvents is low. Acrylic coatings should not be used for PCB protection where exposure to stronger solvents, high-temperature work conditions or other harsh operating environments are expected.
Epoxy offers a strong, durable, easily-applied protective film, with good dielectric properties that withstand harsh operational conditions. This is evident through its exceptional resistance to abrasion, chemicals and humidity; water migration beneath epoxy films is possible, potentially causing delamination, corrosion and performance degradation. Epoxy can shrink during the curing process. It is difficult to remove, requiring a soldering iron for most repair/rework, processes that can damage the PCB.
Silicone conformal coatings work through extreme temperature differences sufficient to cause PCB-failure for most other coatings. Silicone is also among the easiest to apply and re-work; it cures smoothly and in about one hour at room temperature. Silicones have weak resistance to solvents, making rework relatively easy. However, the required thickness of efficient silicone films makes them unfeasible for use with tight clearance tolerances or solder joints unable to support stresses resulting from the weight and bulk of thicker coating layers.
Very resistant to chemical solvents, urethane provides better tin whisker mitigation properties than competing wet coatings. While tough to rework, urethane’s hardness provides good mechanical wear under normal functional circumstances. However, the rigidity of urethane’s high-level abrasion resistance/mechanical strength can weaken the coating’s integrity under high vibration. Urethane does not work well in operating conditions that exceed 125ºC.
Chemically-inert, CVD-applied Parylene has the best solvent/temperature-range resistance of all coating types. Truly conformal and uniform, Parylene adapts to any PCB topography without pooling or coverage-gaps. Transparent and colorless, Parylene has high dielectric strength and requires no curing. Coatings are ultra-thin, successful in the nanometer range, resisting chemicals, corrosives, moisture and solvents. PCB function and performance is protected through most operational conditions; thermal expansion is minimal. Drawbacks include higher production costs and limited throughput. Specialized equipment and materials are required for CVD. Difficult to remove, it must be abraded from the PCB, which could cause board-damage.
Each of the five film types has unique properties Conformal coating selection should be dependent on the material’s performance attributes and the PCB’s performance requirements/operational environment,
Selecting the wrong conformal coating can lead to failures in the field and costly redesigns of products. The right coating type and application method significantly reduces risk of failure. If you are looking for conformal coating services for PCBs, contact SCS today.