<< View SCS Blog
Can Parylene Be Layered?
Multilayer conformal coatings are advantageous in resolving diffusion or stability issues. A vast amount of knowledge is available in the literature about the use of multilayered stacks of Parylene and stacks making use of different intermediate materials such as ALD, metals and so on. Use of multiple layers of Parylene C was most commonly reported for medical implants [1].
Adhesion
Surface energies of materials affect the molecular force of attraction. High surface energy (HSE) leads to a strong molecular attraction and such surfaces are consequently easier to bond to, whereas a low surface energy (LSE) means a weak molecular attraction [2]. Most polymers possess low surface energy, lacking polar functional groups on their surface that would otherwise create optimum bonding. In the absence of functional groups the result is surfaces that are difficult to bond to [3]. The LSE of Parylene can pose a challenge to get optimum adhesion. At the same time, it also makes it an excellent protection layer against oxidants, corrosives. Parylene C has a contact angle of ≈90 degrees [4].
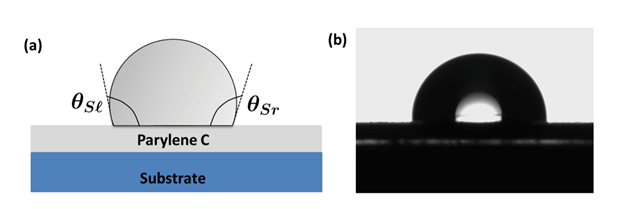
Parylene/Parylene Interface
As explained above, the common issue for Parylene on top of Parylene is the adhesion problem. While not common, in-situ multilayer Parylene coating can be completed without breaking vacuum, eliminating this issue. A typical case, however, is that the Parylene layer is exposed to the outside world for other processes, which results in the oxygen termination of the remaining free radicals as well as the deposition of organics on the surface of the base Parylene layer, resulting in additional adhesion issues. In order to deposit Parylene on Parylene multilayers with a process that breaks vacuum conditions between layers, the initial Parylene surface must be clean and surface-activated to be successfully formed.
Further cleaning and surface treatment such as oxygen plasma is often required to properly prepare the base Parylene layer. In one of the studies, annealing at 200°C (above the glass transition temperature of Parylene-C) was shown to improve the adhesion force between two Parylene C layers. At 200°C recrystallization and intermolecular mixing increases. It is important to note that the glass transition temperature of Parylene has been reported to be in the vicinity of 90°C. Minimizing the use of high temperature (>100°C) processes in the presence of oxygen (i.e. in air) can prevent oxidization, thermal stress, the formation of gas bubbles, or irreversible changes to Parylene morphology [5]. A number of tests have been done on the adhesion of Parylene to Parylene using different surface treatments as shown in the schematic that follows. The process begins with a silicon wafer which is cleaned by a buffered hydrogen fluoride solution to remove native oxides, followed by the deposition of the first Parylene layer. Among the six methods indicated in the schematic, the use of propylene carbonate was found to be most useful by the researchers.
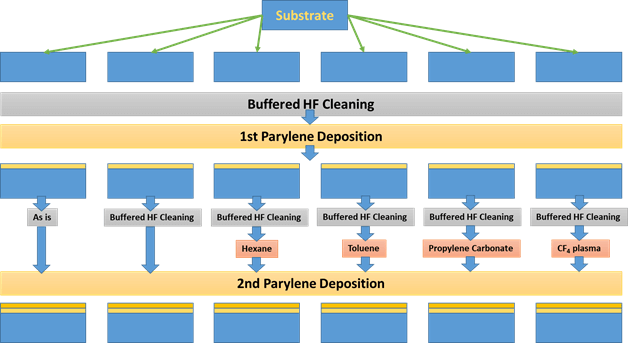
Parylene/Intermediate Layer/Parylene interfaces: Polymer, ALD, Metal, Oxide, Nitride etc.
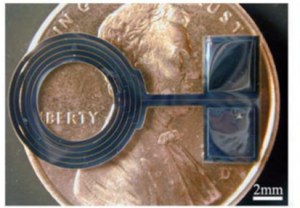
The adhesion of Parylene on top of other materials is successfully accomplished with advanced adhesion technologies, but can also require alternative pre-processing of the Parylene layer. Different methods have been proposed in the literature: Silicon XeF2 surface roughening (with 6.5 μm of silicon removal), Parylene anchoring using advanced DRIE techniques, Parylene melting at 350°C and A-174 adhesion promoter were suggested [6].
It has been demonstrated that Parylene suffers from poor adhesion to noble metals, gold and platinum, particularly with traditional silane adhesion promotion processes (i.e. A-174 silane) and especially after challenged with exposure to steam autoclaving. The AdPro family of adhesion promotion technologies solves this problem and is available to SCS coating service customers. This newer technology additionally overcomes issues observed when multilayered structures are soaked in wet environments. Some reports suggest weak adhesion between different layers can lead to catastrophic failure of Parylene devices due to electrical shorts and delamination. Thus, implementing the appropriate adhesion technology is critical to the success of advanced devices.
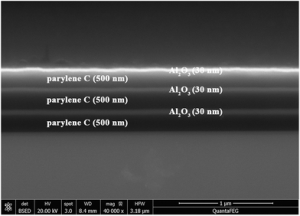
Atomic layer deposition (ALD) of Al2O3 was scientifically shown to be feasible and was reported to form a good bond at the interface between ALD- Al2O3 and the Parylene C layer [8]. ALD+Parylene multilayer coatings are also available from SCS and have demonstrated superior barrier protection for highly sensitive devices.
In conclusion, multilayers of Parylene/Parylene or Parylene/material systems are becoming more mainstream with improved service capabilities seen in recent years. Coating experts carefully consider critical parameters while choosing materials to give the optimum performance as well as surface treatment conditions to result in the needed levels of adhesion. Successfully achieving this will help avoid delamination and resultant catastrophic failure.
References
[1] D. Ziegler, T. Suzuki, and S. Takeuchi, “Fabrication of Flexible Neural Probes With Built-In Microfluidic Channels by Thermal Bonding of Parylene,” J. Microelectromechanical Syst., vol. 15, no. 6, pp. 1477–1482, Dec. 2006, doi: 10.1109/JMEMS.2006.879681.
[2] “What Does Surface Energy Mean and Why Is It Important?,” BDK, Aug. 01, 2018. https://www.bdk.uk.com/2018/08/surface-energy-why-important-adhesive-selection/ (accessed Jun. 25, 2020).
[3] F. Awaja, M. Gilbert, G. Kelly, B. Fox, and P. J. Pigram, “Adhesion of polymers,” Prog. Polym. Sci., vol. 34, no. 9, pp. 948–968, Sep. 2009, doi: 10.1016/j.progpolymsci.2009.04.007.
[4] C. Chindam, A. Lakhtakia, and O. O. Awadelkarim, “Surface energy of Parylene C,” Mater. Lett., vol. 153, pp. 18–19, Aug. 2015, doi: 10.1016/j.matlet.2015.04.009.
[5] J. Ortigoza-Diaz et al., “Techniques and Considerations in the Microfabrication of Parylene C Microelectromechanical Systems,” Micromachines, vol. 9, no. 9, Art. no. 9, Sep. 2018, doi: 10.3390/mi9090422.
[6] J. H.-C. Chang, B. Lu, and Y.-C. Tai, “Adhesion-enhancing surface treatments for parylene deposition,” in 2011 16th International Solid-State Sensors, Actuators and Microsystems Conference, Jun. 2011, pp. 390–393, doi: 10.1109/TRANSDUCERS.2011.5969484.
[7] N. Islam, Microelectromechanical Systems and Devices. BoD – Books on Demand, 2012.
[8] J. Njeim et al., “Effect of the Al2O3 Deposition Method on Parylene C: Highlights on a Nanopillar-Shaped Surface,” ACS Omega, Jun. 2020, doi: 10.1021/acsomega.0c00735.
[9] J. Wu et al., “Efficient multi-barrier thin film encapsulation of OLED using alternating Al 2 O 3 and polymer layers,” RSC Adv., vol. 8, no. 11, pp. 5721–5727, 2018, doi: 10.1039/C8RA00023A.