<< View SCS Blog
Can I Solder Through Parylene?
Parylene: Properties and Processes
Conformal coatings are applied to printed circuit boards (PCBs) and other sensitive electronics to protect their components and electrical function. Parylene conformal coatings provide these assemblies superb security from electrostatic discharge, and additional performance advantages, including:
- Biostability
- Dependable corrosion/moisture resistance
- Good dielectric strength/high-frequency properties, with diminished dielectric constant
- High bulk/surface resistance
- Lowered kinetic/static coefficients of friction
- Protection from chemicals/solvents, salt spray, temperature fluctuations,and vibration
These characteristics are adaptable to a wide range of as aerospace, defense, automotive, consumer, industrial and medical applications.
Parylene’s distinctive chemical vapor deposition (CVD) method of film application is one source of these performance advantages. Unlike the brush, dip or spray processes used to apply pre-synthesized liquid coatings – acrylic, epoxy, silicone, urethane – to substrates, CVD transforms solid Parylene into a gas, which synthesizes during transformation onto targeted surfaces as a conformal coating. Implemented within a specially designed vacuum chamber held at room temperature, Parylene’s gaseous state seeps into a substrate’s surface and polymerizes, essentially growing the protective layer molecule by molecule. Length of exposure to the vaporized XY determines coating thickness, which grows incrementally with prolonged contact. The resultant conformal coating adheres to any PCB/assembly configuration, both internally and externally, generating exceptional protection.
Soldering Parylene
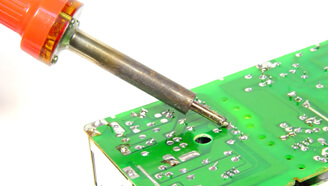
Once applied, Parylene is very difficult to remove, enhancing its protective/barrier utility. With regard to solder already in place on PCBs, Parylene coatings will extend operational lifetime by as much as 100%, doubling the functional use of an assembly’s soldered joints and components.
Parylene also significantly limits the development of tin whiskers — microscopic conductive fibers growing from an assembly’s tin surfaces, which can cause serious problems to electronic performance and shorting during use, which renders the assembly useless.
Solders composed at least partially from lead – the source of tin – are frequently used on PCBs, which can also have tin-plated surfaces. In comparison to liquid coatings, Parylene offers considerably better tin whisker protection, limiting its development while maintaining electrical functional, with much thinner layers of film.
These are instances of Parylene working in conjunction with already-soldered parts. Like other conformal coatings, application of Parylene is completed after boards have been manufactured; it cannot provide optimal performance for assemblies that require further soldering or other modification after film application. Yes, Parylene can be successfully soldered through at any point after the conformal film has been applied, but doing so forces other issues emanating from exposure of the already-covered substrate.
Because Parylene is so difficult to remove, soldering the coating surface should be confined to its removal, cases where PCB components are malfunctioning or other repair issues emerge. Parylene’s CVD application method combines with its relative film durability to negate use of most removal methods available to liquid coating materials. For instance, Parylene cannot be simply be submerged in a solvent bath for removal, as is the case for substrates coated with acrylic. Parylene removal is more difficult, requiring application of micro-abrasive, mechanical or focused heat (thermal) technologies.
Despite difficulty removing Parylene, concentrating extreme heat onto its conformal films will melt or burn through the film layer to the substrate. Thermal breach of the coating will occur regardless of its thickness. How long the process takes is a function of coating thickness, and additionally, Parylene has a higher melting point than many plastics, ranging from 290°C for Parylene C to over 500°C for Parylene HT®. Under these circumstances, thermal application may take some time. Soldering will generate sufficient heat for these purposes; the handheld iron can be explicitly directed toward a designated region of the film’s surface.
This method of Parylene removal is, however, less advantageous than abrasive or mechanical methods. Soldering through Parylene can cause discoloration, yield residues, raise toxic fumes dangerous to the operator and, most significantly, damage PCBs and temperature-sensitive substrates causing dysfunction or assembly failure.
Parylene can be soldered through and it is suggested that the highest-quality soldering iron under a vacuum hood be used for these purposes. Be aware of the consequences to the coating and perhaps the assembly itself if appropriate care is not taken. Soldering processes should be confined to coating removal or assembly repair, since the heat generated by soldering can damage the substrate and its contents.