<< View SCS Blog
Benefits of Parylene Coatings for Electronics
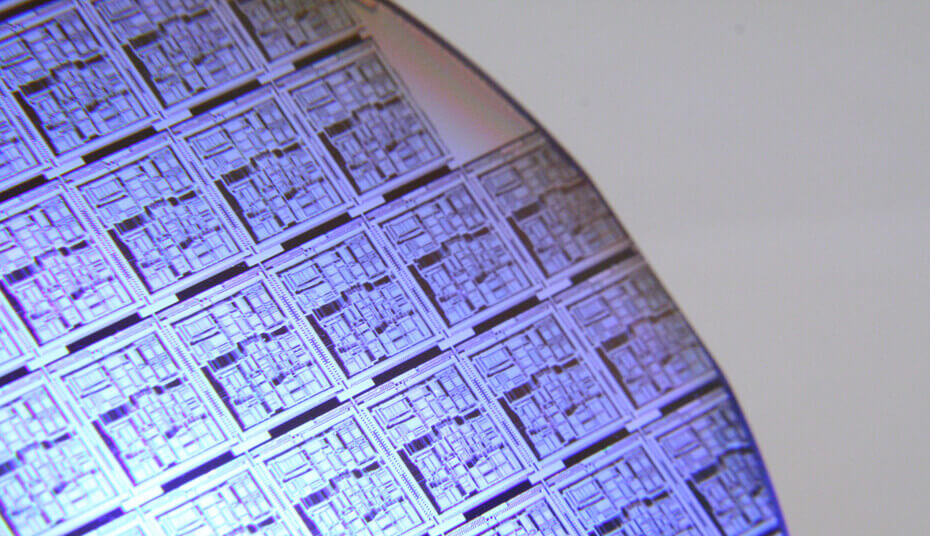
Parylene conformal coatings are some of the best protection options available for printed circuit boards, multi-layer assemblies and other electronics. The coatings are applied through a vapor phase deposition (VPD) process that transforms the solid Parylene raw material, known as dimer, into a gas, enabling complete coverage of the substrate’s surface including deep penetration into small crevices. The Parylene film layer is uniform, and the polymer can be applied to almost any substrate material.
In addition to their molecular-level deposition that results in highly-reliable, protective coatings, additional advantages of Parylene conformal coatings for electronics include:
- No curing process
- Nonconductive properties
- Ultra-thin layers, usually measured in microns
- Durable against environmental factors
- Resistant to moisture and chemicals
- Comprehensive, pinhole-free coverage
- Stable in temperatures up to 350°C long-term
The protective features of Parylene conformal coating are advantageous for many electronic systems, including:
- Wafers
- Circuit boards
- Power supplies
- I/O and PCI modules
- Backplanes
- Multi-layer assemblies
- Microelectromechanical Systems (MEMs)
- Sensors
- Power converters and supplies
- Batteries
- LEDs
In addition to Parylene conformal coatings, SCS offers a wide range of coating solutions to meet the diverse needs of electronics manufacturers.
- Various coating types: In addition to numerous Parylene variants, SCS offers liquid and multi-layer coatings, including silicones, epoxies, acrylics, urethanes and ALD coatings.
- Coating removal and repair: SCS is able to provide coating removal and repair as needed for customers.
- Industry-leading applications engineering: SCS’ diverse team of applications engineers has over 50 years of experience in coating various products across industries. These teams stand ready to assist customers in helping to select the best coating option for their product.