<< View SCS Blog
Parylene Delivers Critical Barrier Protection for Medical Cables
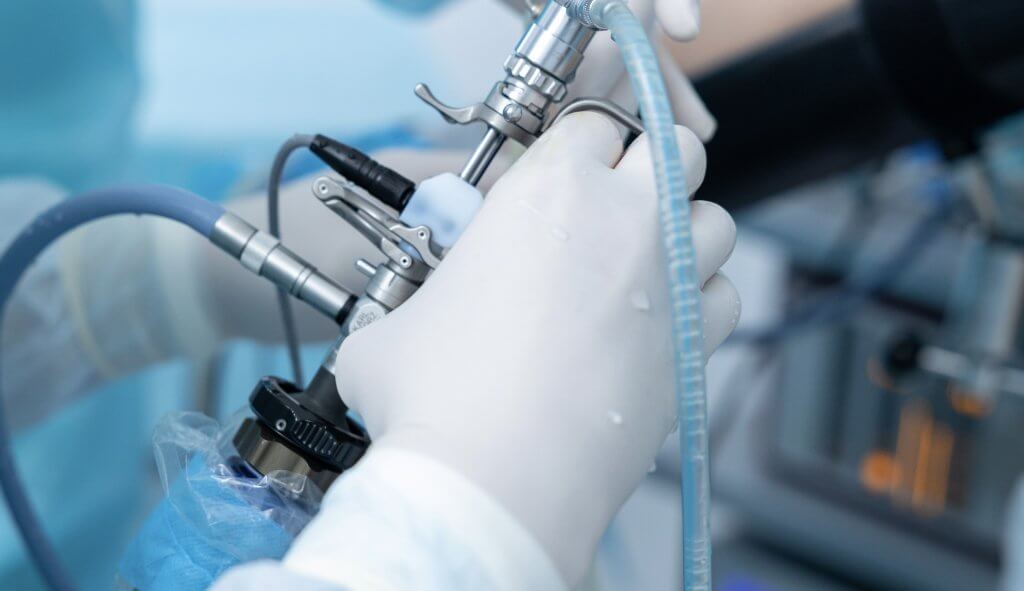
Today’s specialized medical cables are complex components of larger systems used in all phases of preventative, diagnostic and therapeutic medical care. The essential and functional components of a medical cable include high-performance connectors, sheaths or jackets, and conductive lines. To meet and exceed the demanding needs of doctors, nurses and medical technologists, conformal coatings often increase the reliability of a functioning cable and make it more user-friendly by reducing friction, sealing porosity and providing barrier protection. The properties of the coated cable, including its biocompatibility, remain unchanged after common sterilization techniques.
Reducing Friction
Many cable jackets are elastomeric, and, in their basic state, can often have surfaces with high levels of friction that prevent them from sliding smoothly over a variety of surfaces that the cable might encounter, including surgical gowns, bed coverings, patient drapes (with or without adhesives), other cables, surgical tools and trays as well as other instruments. As a surgeon uses a powered tool that requires a cable, he or she may move the tool in a way that drags the cable across one surface or another. An uncoated cable might generate resistance to the movement or even hang up on the surface, causing the surgeon to adjust to the resulting aberration. Unwanted disturbances can also occur if other personnel in the surgical suite are required to rotate the operating table so that the surgeon can optimize his or her approach to the targeted area. “Sticky” cables can cause interruptions to the smooth completion of critical motions necessary for the best possible outcome for the patient, whereas the right modification to the cable surface can have a positive functional impact on the overall procedure.
Sealing Porosity
Since most cables are cleaned and sterilized for reuse, minimizing places where contaminants can hide is essential from the standpoint of health, safety and cost. Even though the jacketing or sheathing of a cable might be biocompatible, most materials used have a high degree of microscopic porosity due to the nature of the material compound itself and its method of manufacture. This porosity provides the perfect hiding place for biological and non-biological contaminants that must be eliminated prior to initial or repeat use. A Parylene conformal coating, for example, applied to the cable will seal the porosity of the sheathing, minimizing the places where unwanted contaminants reside; this results in a surface that can be more effectively cleaned and sterilized. The unique vapor deposition-polymerization process used to form Parylene films achieves this when its molecules penetrate the micro-porosity of the substrate surface, forming the film within the micro-structure and filling the smallest of pores, thus minimizing the deepest hiding places for contaminants. This high performance coating results in improved cleanability of the surface in preparation for the cable’s next critical assignment.
Barrier Protection
The useful life of cables is often impacted by the negative effects of cleaning agents used on the sheathing and connector housing materials. A coating that possesses outstanding chemical-barrier properties can provide a significant hedge against the premature degradation of exposed surfaces due to the use of necessary cleaning agents. In addition to cleaning, critical reuse components are often required to undergo sterilization and repackaging to ensure that all instruments and equipment entering a sterile area have met the necessary cleanliness requirements. Parylene coatings provide a biocompatible barrier that can withstand the harsh cleaning agents and sterilization processes needed to put medical cables back into use.
Parylene Conformal Coatings for Medical Use
There are four variants of SCS Parylenes used in the medical market: Parylenes N, C, ParyFree® and Parylene HT®. Parylenes are extremely lightweight, and, at the optimum thicknesses, offer excellent barrier properties without adding dimension, stiffness or significant mass to high-performing medical components. Since all Parylene coatings are free of fillers, stabilizers, solvents, catalysts and plasticizers, there is no outgassing from the film and leaching concerns are eliminated, maintaining a preferred surface for components from surface devices to implants. When it comes to specialty medical cables, reducing friction, sealing porosity and adding critical barrier protection can be accomplished with the use of high-performance Parylene conformal coatings, resulting in improved performance and reliability. For more information on how SCS Parylenes can benefit medical cables, contact Dick Molin at 317.244.1200, ext. 0271, or dmolin@scscoatings.com.
Global Coverage Issue 91, Spring 2022