<< View SCS Blog
Benefits of Automotive Conformal Coatings
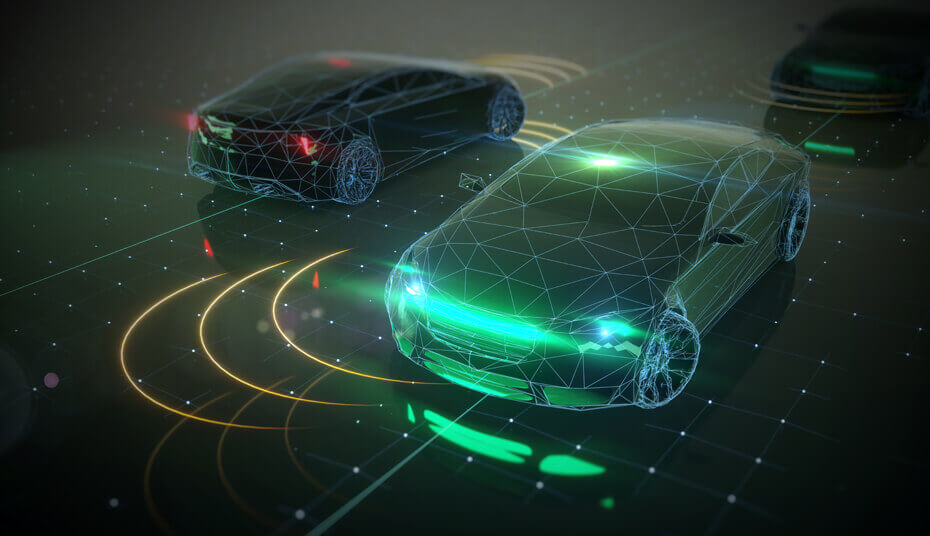
Silicone and Parylene coatings are among the best options on the market to protect automotive electronics and components. Silicone coatings are applied by dipping, brushing or spraying, and Parylene coatings are applied by chemical vapor-based deposition (CVD). Advantages of each coating are listed below.
Advantages of silicone coatings for automotive electronics include:
- Impact and shock absorption
- Thermal resistance (> 200°C)
- Moisture and corrosion resistance
- Flexible and soft
- Adherence to printed circuit board (PCB) topography
- Ultraviolet (UV) light resistance
- Quick curing time
- Easy to rework
Benefits of Parylene coatings for automotive electronics include:
- Lightweight and ultra-thin, adding minimal mass to components
- Moisture and corrosion resistance
- Dielectric protection against current fluctuations
- Chemically-inert for protection against salt, antifreeze, gasoline and brake fluid
- Stable in fluctuating temperatures: -165°C to 450°C (short-term)
- Excellent adhesion to numerous materials
- Molecular deposition provides complete coverage of all topographies, including inside crevices
- Bubble and pinhole-free surface
- Optical clarity
Conformal Coatings for Automotive Electronics
Choosing the best conformal coating for your automotive application is critical as the right protection improves performance and limits costly warranty claims. For five decades, conformal coatings have increased the reliability of these vehicle electronics and more:
- Emission controls
- Fluid monitoring
- Powertrain mechanics
- Lighting
- Sensors
- Fuel systems
- Batteries
- Digital displays
- Fuel cells
- Power controls for the windows, seats, mirrors, doors, sunroof, etc.
- Tire pressure gaskets, seals and sensors
- Antilock brakes control
- Connectors
- Monitoring systems
Contact SCS today for more information on conformal coatings and how to select the best coating option to protect your automotive electronics.