<< View SCS Blog
Conformal Coating for Automotive Applications
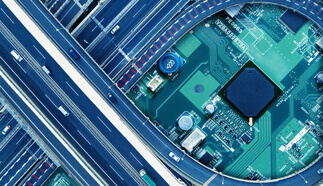
Parylene is becoming one of the most useful tools in an automotive design engineer’s arsenal. From protecting internal sensors and circuit boards to keeping LED indicator lights bright and color-accurate, Parylene conformal coatings are an important part of protecting today’s sensitive automotive electronics.
Parylene Basics
Parylene is a unique conformal coating in that it gets applied in a vacuum while in a gaseous state. This allows it to truly cover every surface on a coated item with a complete and pinhole-free coating. At the same time, the coating can be impermeable at anything above 1.4 nanometers (nm), which is more than thin enough to be suitable for areas that require tight tolerances, such as micro-electro-mechanical systems (MEMS).
Unlike some other coatings, Parylene is also extremely tough. It can easily endure the cold of a vehicle in Antarctia, the heat of an interior exposed to the desert sun in summer or the temperature of an engine’s combustion chamber. The coating is also so chemically inert that it can withstand exposure to brake fluid, antifreeze, salt air and even automotive chemicals with solvent properties like gasoline.
Circuit Boards
Today’s cars have around 100 million lines of code and intricate circuitry with numerous microprocessors. Those circuit boards must be rugged, small and extremely reliable. Coating them with Parylene solves two problems. First, it provides protection from the harsh atmosphere inside a car, shielding the electronics from chemical fumes, cooling fluids, temperature variations and particulate matter that could damage it or gradually coat its traces, causing thermal issues or short circuits. Second, Parylene is also an excellent dielectric that provides insulation. This allows traces on the PCB to be closer together, shrinking the component size. It also reduces the risk that other nearby electronics will interfere with the coated board’s operation.
MEMS
Vehicles are equipped with intricate microelectronics and sensors that gauge performance, enabling recalibration for enhanced efficiency or power output. These sensors can be exposed to extremely harsh conditions. Battery management systems (BMS) need cooling fluids that are nearby to electronics and sensors. Bus bars for transferring power need to maintain electrical isolation for fluids and moisture. Fuel lines driven by high-pressure pumps contain flow sensors, while engine components have temperature sensors. Tire pressure sensors and inertial sensors are exposed to dust and vibration, while manifold pressure sensors have to withstand searing temperatures. Parylene protects these small parts from damage. It can also be masked to leave sensor surfaces that need to be exposed uncoated.
Polymers
The gaskets, seals and hoses throughout cars also benefit from Parylene coating. As with other parts, Parylene protects them from both the harsh conditions inside the car, as well as the chemical properties of the fluids or compounds that they carry or hold in place.
Parylene is also an excellent lubricant. This helps those compounds flow past the seal without turbulence. It also can make coated components easier to install or to remove for service.
LEDs
LEDs, known for their durability, exceptional light output and energy efficiency, are key for automotive applications. While UV sensitivity poses a challenge, UV-stable coatings, including a specialized Parylene formula from SCS, provide crucial protection against UV damage to ensure lasting performance.