<< View SCS Blog
Parylene Protection of Wearable Devices
Wearable devices have become an integral component of everyday life, with expanded uses for many conventional activities. Advanced consumer electronics and med-tech – ranging from external exercise monitors for human performance to implanted cardiac pumps, defibrillators and deep-brain sensors – represent only a fraction of wearable medical devices currently applied for healthcare and treatment. Smartphones and watches can be found everywhere; smart fabrics are used with increasing frequency for clothing and textiles. Wearables reflect the expanding scope of the Internet of Things in most areas of human endeavor.
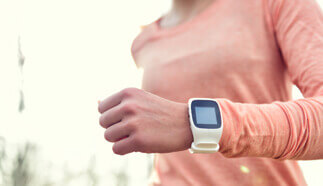
As use of wearables grows, manufacturers try to determine the optimal mix of form, function and technology that will encourage further consumer and professional application of the devices. In consumer health and healthcare, wearables provide a range of status indicators (heart rate, physical activity levels, etc.) that monitor individual’s engagement of healthful (or unhealthy) activities. In addition to focusing on improving their functional technology, battery life and consumer fashion, the need to safeguard wearables performance is a prominent concern. Wearable devices rely on advanced technologies that necessitate conformal protection within their operational surroundings. Parylene coatings stand out as the optimal choice for safeguarding devices in nearly all scenarios.
Parylene as a Safeguard of Wearable Functionality
Wearables of all kinds possess sensors; these sensors include items like artificial magnetic conductors (AMCs) and light-emitting diodes (LEDs) that support wearable functionality while recording their own and their wearers’ activities. This is particularly the case for microelectromechanical systems (MEMS) and nanotech (NT) sensors, which can require both exceptional protection from their functional environments and micro-level security due to their extraordinarily small physical dimensions.
Parylene conformally coats even the smallest and most complicated item with a resilient, ultra-thin film, generating functional superiority for safeguarding MEMS/NT.
Examples of wearable device applications that utilize Parylene conformal coating include:
- Parylene device-level water/sweat resistance for bio-sensors integrated into wearables
- Parylene protection of biomedically applied inkjet-printed microwave antenna, AMCs, and related assemblies from ambient body-generated humidity.
- Parylene protection of substrate integrated waveguide (SIW) on paper substrates used in wearables.
- Parylene films securing the performance of ultrafine pixeled, full-color LEDs basic to wearable electronics; these deformable LEDs depend upon conformal integration to their curvilinear surfaces, and benefit from Parylene’s nano-level films — applied at 500-nm-thick, the films protect against oxidation, while generating an ultra-flat surface across a variety of substrate topographies
While Parylene’s effective, thin-coat dielectric properties obstruct EMF and RF interference, they can also interfere with a wearable’s ability to accurately measure, record and report its own or the wearer’s performance and activities, unless appropriate steps are taken during production
In this regard, masking prior to Parylene chemical vapor deposition (CVD) prevents it from depositing on wearable sensors and related components, securing efficient operation, while retaining the protection of conformal coating for the remainder of the unit.
Parylene’s collective properties support the real-world performance expectations inherent in wearables. They generate a truly conformal film that resists water and body sweat, as well chemicals, corrosives and solvents, protecting the device’s function and performance whether worn on the body or implanted internally. Parylene performs reliably at normal body temperature and is able to withstand temperatures ranging between -200°C and 350°C with no appreciable operational degradation.
Biocompatible, micro-thin Parylene is exceptionally lightweight, assuring non-irritating performance, whether worn against the skin or implanted; dry- film lubricity further adds to comfortable functionality. Parylene coating prevents gasses from entering the wearable, resisting physical abrasion and impact as well, a matter of concern, since wearables are often worn on the body and can be exposed to real-world environmental conditions; these include but are not confined to persistent bodily excretions, direct sunlight/UV rays, variable electrical signals, acidic/salt solutions/sprays and motion/vibration.
Conclusion
The market for wearable sensory and related technologies for both consumer products and in healthcare is expected to grow significantly through the mid-future. Parylene conformal protection should evolve with continued development of both wearable and Parylene technologies. For instance, innovations in wearable medical technology will further explore the intersection between physical and digital worlds, as an increasingly standard provision of patient care; a similar direction is anticipated for the future’s wearable consumer products.
All wearable devices are only as functional as the protection they receive. Effective at thicknesses measured in microns, Parylene provides optimal conformal security for wearables of all kinds. In addition to exceptional water resistance, Parylene conformal films also secure wearable devices against sweat, EMF/RF signals, humidity, caustic solutions emanating from both inside and outside the body, and chemical exposure. Parylene’s protective properties makes it uniquely suited to provide this range of safeguards for wearables.