<< View SCS Blog
Dielectrical Performance and Strength of Parylene
A primary function of all conformal coatings is maintaining sufficient insulation and avoiding dielectric breakdown while protecting printed circuit boards (PCBs) and related electronic assemblies. Providing a completely homogeneous coating surface, Parylene (XY) conformal coatings are exceptionally corrosion-resistant, dense and pinhole-free. Among other performance advantages, ultra-thin XY protective films offer superior dielectric properties. Dielectric substances maintain electrical insulation and have the potential to store energy because they support electrostatic fields that release only low levels of thermal energy.
Maintaining electrical performance factors is necessary for ongoing PCB-operation; preventing dielectric breakdown (DB) is essential. DB results from a buildup of electrical charge within a PCB that surpasses a coating material’s dielectric strength (DS – its electrical performance limit). In such cases, negative- and positively-charged electrons within the assembly are simultaneously pulled in opposite directions, ionizing the environment. It is transformed from an insulator to a conductor, generating sparks and similar electrical disturbance which leads to dysfunction and breakdown.
Obviously, avoiding DB is essential for effective conformal coating, requiring suitable DS. XY films generate increased DS between conductors enabling smaller, more compact PCB design. DS is a measurement of a conformal coating’s insulation effectiveness. Parylene’s lower dielectric constants in comparison to liquid conformal coatings indicate:
- Enhanced ability to withstand intense electrical fields
- Significantly limited film devolution
- Maintained assembly performance under operational conditions characterized by intense electrical activity
Conformal coating materials demonstrating fewer extractible ionic impurities and greater hydrophobicity have superior DS. In terms of measurement, higher-valued ratings (7,000) indicate a particular coating material will resist electrical breakdown better than one whose DS value is lower, (2,000). Compared to liquid coatings, Parylene’s higher DS shows considerable advantage generating appropriate dielectric protection for PCBs. In addition, XY’s lower DCs represent diminished concentrations of electric flux, resisting the impact of current fluctuation within the assembly. One of Parylene’s most significant advantages is the ability to withstand substantial electrical activity, maintaining its structural integrity and assembly performance. Both DS and DC values vary according to coating material, and can also vary within material type. Table 1 provides DS/DC values for Parylenes N and C, and the major liquid coatings.
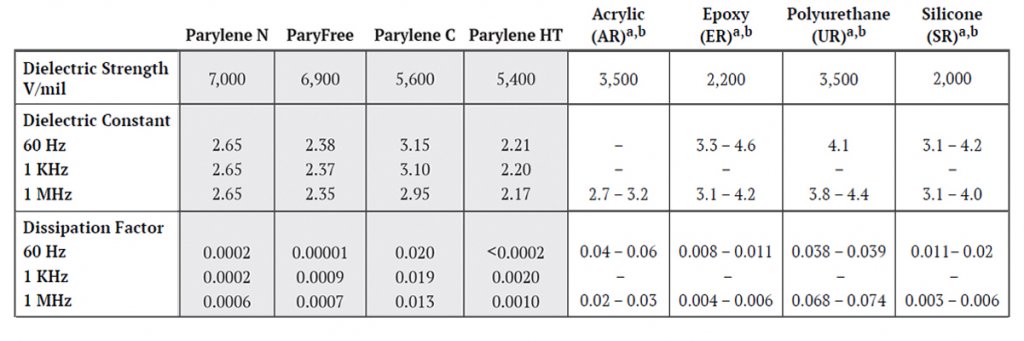
DC values exceeding 3.0, indicate inappropriate molecular response to the alternating current/field, and diminished ability to perform under conditions of electrical stress and fluctuation.
DC values exceeding 3.0, indicate inappropriate molecular response to the alternating current/field, and diminished ability to perform under conditions of electrical stress and fluctuation.
XY’s DC ratings are better than those for liquid coatings, representing enhanced performance. The same results pertain to DS; Parylene ratings are better in all cases, compared to wet conformal films, whose lower values indicate excessive thermal generation, undesirable for sustained conformal coating function.
DC readings for other Parylene types range between 2.17 – 3.15.
Dielectric loss registers dissipation factor, for levels of internal heat within conformally coated substrates; Here again, XY performs admirably.
In both cases, XY coatings exceed professional performance standards for dielectric control. As a lower DC conformal film, Parylene’s weakly-bonded molecules produce dependable buffers between a PCB and its operating environment. Polarized by electrical charges, XY:
- Resists electrical conduction
- Enriches its utility as a coating for high-speed electrical assemblies
- Exceeds wet coatings’ performance
To further illustrate, the wet coatings identified on Table I each register DCs larger than 3.0. Thus, the possibility of circuit-speed variance increases, a development that can interfere with the operation of any higher frequency component. In addition, DS of liquid coatings is lower, reducing their ability to maintain performance – adhesion to assembly surfaces and consistent component protection; they are more likely to break down during prolonged contact with intense electrical activity. Unlike XY films, those composed of acrylic, epoxy, silicone or urethane are prone to dielectric breakdown and current conduction, especially with the passage of time. Parylene reliably sustains an assembly’s electric field without conducting electricity.