<< View SCS Blog
4 Aerospace Applications of Parylene
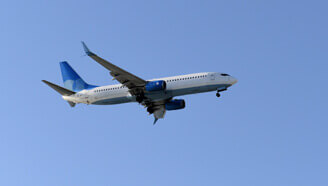
Superior to liquid coatings like acrylic, epoxy, silicone and urethane, Parylene conformal films offer unparalleled protection for aerospace printed circuit boards (PCBs) and related electronic assemblies. Their complete encapsulation conforms entirely to all device surfaces – flat, round, creviced or edged, while adding almost no weight to the covered device.
These properties are largely the result of Parylene’s unique chemical vapor deposition (CVD) process, which applies gaseous Parylene deep within PCB surfaces, generating an authentically conformal, micro-thin coating. Parylene coatings also:
- Adhere well to most surfaces
- Minimize ionic conduction at the substrate interface
- Strengthen solder joints, circuit links and wire bonds
- Have a low dielectric constant, minimizing high-frequency loading
Parylene is truly conformal to all surfaces, even in exceptionally small spaces. Additionally, Parylene is highly resistant to fungi and solvents.
Parylene is a military specification conformal coating (MIL-I-46058) suitable for aerospace assemblies, which are seldom adequately protected by standard liquid brush-on, dip and spray coating methods. In general, liquid coatings that work without fail for consumer devices lack the longer-term, ruggedized resilience required for prolonged aerospace use. Lightweight, highly durable Parylene conformal coatings provide optimal protection, are hydrophobic and can withstand a 144-hour salt spray test, which exceeds the MIL-STD-810F ruggedization standard.
Microelectromechanical (MEMS) Applications
A major aerospace application for Parylene conformal coatings is protecting MEMS, nano-tech and other multiple-layer circuit instrumentation. These typically include cockpit, engine management, flight control, and sensor systems located throughout the in-flight vehicle. In these situations, PCBs benefit from the exceptional thermal stability generated by Parylene film, ranging from 80°C, long-term, to 450°C, short-term (<24 hours).
Parylene’s low dielectric constant and dissipation features allow:
- Dielectric insultation, supporting true and undistorted signals for wireless devices
- Interfacing cross-device control-to-human and control-to-control communications
- Applicable to electrical/fiber-optic interconnect systems used to manage deployment of failure-critical armament, navigation and radar systems, among other similarly important applications
In particular, Parylene HT® offers an advanced aerospace solution for instrumentation requiring superior protection for enhanced performance reliability.
Ultraviolet (UV) Protection
Prolonged exposure to high energy UV radiation can generate extensive surface damage and lead to eventual equipment malfunction of, for instance, electrical, light-generating LED assemblies within. Newer high-temperature, UV-stable Parylene formulations (Parylene HT) meet the challenge of UV degradation to aircraft LED-lighting, preventing LED-yellowing and surface discoloration from prolonged exposure to UV radiation. By filtering UV light from the coated item, Parylene protects internal LED assemblies from operational malfunction caused by UV radiation, sustaining their performance as energy-efficient, long-lasting sources of cabin, landing gear and navigation lighting.
Parylene provides lightweight conformal, pinhole-free covering that generates enhanced LED protection through prolonged exposure to aerospace environments, at minute surface thicknesses ranging from 500 angstroms to 75 microns.
Communications/Electronics
Aerospace electronic systems are frequently subjected to extremes in temperature and vibration, as well as the incursion of in-flight particulates of questionable origin. Computerized and radio internal/external communications equipment require highest level protection to assure ongoing function. Additional effected electronics systems include:
- Flight control units
- Inertial sensors
- Mother/navigation boards
- Multiple device management software for closed-loop control, image processing, and video data sampling
- Onboard calibration systems
- Telemetry/command systems
- Vision algorithms technology
Parylene adheres mechanically, rather than chemically, to a given substrate, protecting specialized aerospace electrical systems. Its dielectric properties prevent crosstalk and interference for these protected devices.
External Operations
Reliable ruggedized protection is a necessity for circuits situated externally. For instance, aircraft wing/tail applications are subject to rapid-change, non-controlled operating environments, exposed to extreme atmospheric changes. These conditions frequently exceed the security parameters provided by liquid conformal coatings. Parylene coating protects these assemblies, ensuring appropriate function as the aircraft moves from sea level to upper atmospheric operating altitudes, enabling PCBs, sensors and similar devices to perform according to design expectations for both commercial/industrial and military aerospace applications.
Parylene film’s high strength, low permeability, and resistance to temperature extremes make it an effective protector of exposed surfaces such as optical windows, radiation detectors, and radar transmitters. It repels moisture, chemicals and corrosive liquids, simultaneously providing lightweight barrier protection without the significant dimension or mass of liquid coatings.
Conclusion
Parylene coating technologies protect and support aerospace applications, leading to enhanced performance and lifespan of mission critical PCBs, communication devices, power supplies, radar/detection equipment and even satellite electronics.