<< View SCS Blog
Does Parylene make my Product Waterproof?
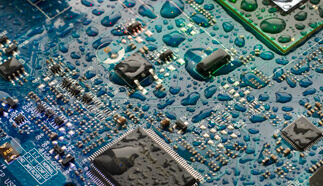
Protecting printed circuit boards (PCBs) and similar electronics from the incursion of water is an essential responsibility of Parylene conformal coating. Suitable Parylene permeation barriers assure no form of liquid passes through to underlying components and that the water vapor transmission rate (WVTR) is minimal. WVTR measures the level of water vapor migration through the applied barrier film, in terms of area and time. Optimal WTVR ratings are represented by lower numerical values. In comparison to liquid coatings, Parylene typically provides lowest-level values, indicating better moisture barrier protection.
Acrylic, epoxy, silicone and urethane coatings can be more quickly affected by water, its vapor and other sources of moisture, including:
- Acid rain
- Mists of other airborne pollutants
- Salt-air
- Chaotic weather
Demonstrating greater moisture barrier management, Parylene also provides protection for implantable medical devices that need to withstand the presence of internal sources of moisture within the body.
Of all Parylene types, Parylene C has the best water vapor barrier properties. Table 1 lists the WVTR of five Parylene types, as well as those for several liquid conformal coatings.
Table 1: WVTR Barrier Properties of Parylene and Liquid Conformal Coatings
Parylene C | ParyFree® | Parylene N | Parylene D | Parylene HT® | Acrylic (AR) | Epoxy (ER) | Polyurethane (UR) | Silicone (SR) | |
WVTR (g·mm)/ (m2·day) | 0.08 | 0.09 | 0.59 | 0.09 | 0.22 | 13.9 | 0.94 | 0.93-3.4 | 1.7-47.5 |
This data demonstrates the superiority of all Parylene types as a barrier against water vapor incursion, in comparison to major liquid coatings. Parylenes C and D have particularly low WVTR-levels. However, it should be noted that some passage through the Parylene film will eventually occur, causing the coating to swell. Parylenes have been tested in accordance with the applicable requirements of IEC 60529, test conditions 14.2.7 and 14.2.8 for IPX7 and IPX8 designations. The uncoated electronics failed during the test, but the Parylene-coated electronics passed both test conditions, functioning normally both during and after testing. These results indicate that Parylene conformal coatings are suitable to protect consumer electronics and other devices against water splash and water immersion per IPX7 and IPX8 test requirements.
Table 2 provides further substantiation of Parylene C’s superior moisture barrier performance compared to ER, UR, SR and TeflonTM materials, following immersion in saline solution of sodium chloride and water.
Table 2: Resistance of Different Polymers to 0.9% Saline Solution
Parylene C | Epoxy (ER) | Urethane (UR) | Silicone (SR) | Teflon | |
Coating Method | CVD | Dip Coating | Dip Coating | Dip Coating | Spraying |
Thickness (microns, μm) | 25 | 100 ± 25 | 100 ± 12.5 | 75 ± 12.5 | 75 |
Time Until Total Breakdown | > 30 days | 6 hours | 6 hours | 58 hours | 6 hours |
The data in Table 2 once again shows Parylene’s water barrier superiority, requiring far longer to be breached by a saline solution (30+ days) than any of the liquid coatings and Teflon at lesser coating thicknesses, 25 μm. If the Parylene coating were expanded to levels of the other listed coatings (75+ μm), the breakdown time would also expand. While cases where protected devices are expected to function in a salt solution for more than 30 days are rare, specialized Parylene conformal coatings can ensure the substrate will remain functional under most harsh operating conditions.
Products that require no-fail functionality, such as those used in aerospace and defense, industrial, medical and telecommunications applications, require stringent water barrier performance for enclosures, gaskets and sealing. Parylene exceeds liquid coatings for water barrier protection. Lightweight and ultra-thin Parylene coatings also improve fuel efficiencies for automotive and aerospace applications and internal positioning for biomedical uses. Parylene meets the requirements of the IPC-CC-830B standard as a hydrolytically-stable conformal coating, requiring higher levels of moisture insulation resistance and humidity-aging testing. Regarding any moisture penetration and interference, this covers operating situations where acid rain, aggressive solvents, atmosphere pollutants, high humidity, intermittent immersion, persistent rain, snow and salt fog, as well as internal environments with high moisture/liquid content are commonly encountered.
Table 3: Water absorption rates
Parylene C | Parylene D | Parylene N | Parylene HT | |
Water absorption (% after 24 hrs) | <0.1 | <0.1 | <0.1 | <0.01 |
Conclusion
Parylene’s moisture barrier properties that support waterproof performance include:
- Very low WVTR for a conformal polymer film
- Minimal liquid water uptake/absorption
- Exceptionally limited ionic permeability; salts pass through the coating slowly and with great difficulty
- Low coating porosity; Parylene CVD forms a pinhole/pore-free coating at a thickness of 5 – 8 microns
- Meets applicable requirements of IPX7 and IPX8 testing