KOOPERATIVE PROJEKTE
Zusammenarbeit mit industriellen und akademische Partnern
Specialty Coating Systems leistet Pionierarbeit auf dem Gebiet der konformen Beschichtungstechnologien und nimmt mit herausragenden innovativen Produkten und Technologien wie ParyFree®, Parylene HT®, Parylene C-UVF® und der AdPro-Adhäsionstechnologie eine führende Rolle in der Branche ein. Seit mehr als fünf Jahrzehnten treibt SCS im Rahmen kooperativer Projekte mit wichtigen Partnern in der Industrie und im akademischen Bereich die Entwicklung neuer Beschichtungstechnologien und erweiterter Anwendungszwecke für Beschichtungen voran.
Comelec, die Schweizer Niederlassung von SCS, arbeitet seit langer Zeit in einer strategischen Partnerschaft mit der in Lausanne ansässigen Schweizer technischen Hochschule EPFL zusammen. Diese Zusammenarbeit hat die Entwicklung eines hochentwickelten Hybrid-Abscheidungsverfahrens für mehrlagige Beschichtungen wie beispielsweise ALD+Parylene-Beschichtungen ermöglicht. Comelec und die EPFL setzen diese erfolgreiche Partnerschaft auch in Zukunft fort und konzentrieren sich dabei auf die Verbesserung der Technologie für implantierbare medizinische Vorrichtungen, die langfristig aktiv bleiben, so genannte AIMDs (Active Implantable Medical Devices).
SEALANT
2020 bis 2024
Das SEALANT-Projekt zielt darauf ab, weiche und für AIMDs sichere Verkapselungstechnologien zu entwickeln, die für bestimmte Anwendungszwecke anstelle der herkömmlichen unförmigen Behälter aus Metall oder Glas verwendet werden können. Die Leistungsfähigkeit der Technologie wird an unterschiedlichen Implantaten untersucht. Diese Untersuchungen schließen sowohl die Anpassung vorhandener Produkte als auch die Verkapselung neuer bahnbrechender mikrooptischer Implantate für die Optogenetik ein.
Bei diesem Projekt werden Parylene und anorganische Materialien in mehreren Lagen übereinander geschichtet, um effektive Barriereeigenschaften zu erzielen. Herkömmliches Parylene gehört in der Medizintechnik schon lange zu den bevorzugten Beschichtungsmaterialien. Mehrlagige Beschichtungstechnologien wurden jedoch bisher noch nicht in großem Umfang auf ihre Eignung für AIMDs untersucht. Das SEALANT-Projekt nutzt diese fortschrittliche Beschichtungstechnologie, um neue Verkapselungsmethoden zu entwickeln, die sich für eine Vielzahl von Produkten eignen und damit die Entwicklung neuer implantierbarer Produkte ermöglichen.
RELIEVE
2018 bis 2021
Das Projekt RELIEVE war darauf ausgerichtet, Patienten mit chronischen Kopfschmerzen durch Neuromodulation zu behandeln und damit eine bioelektronische Lösung bereitzustellen, die frei von den bei Pharmazeutika auftretenden ernsthaften Nebenwirkungen ist. Das extrem miniaturisierte und flexible bioelektronische RELIEVE-Implantatsystem passt sich an die Anatomie des Patienten an und kann in einem schnell abgeschlossenen Verfahren ambulant implantiert werden. Dieses neue Verfahren ermöglichte den Verzicht auf die herkömmlichen voluminösen Implantatgehäuse (aus Metall, Glas oder Keramik). Stattdessen wird ein innovativer, weicher Verkapselungsansatz genutzt, der mithilfe fortschrittlicher mehrlagiger Beschichtungstechnologien verwirklicht werden konnte.
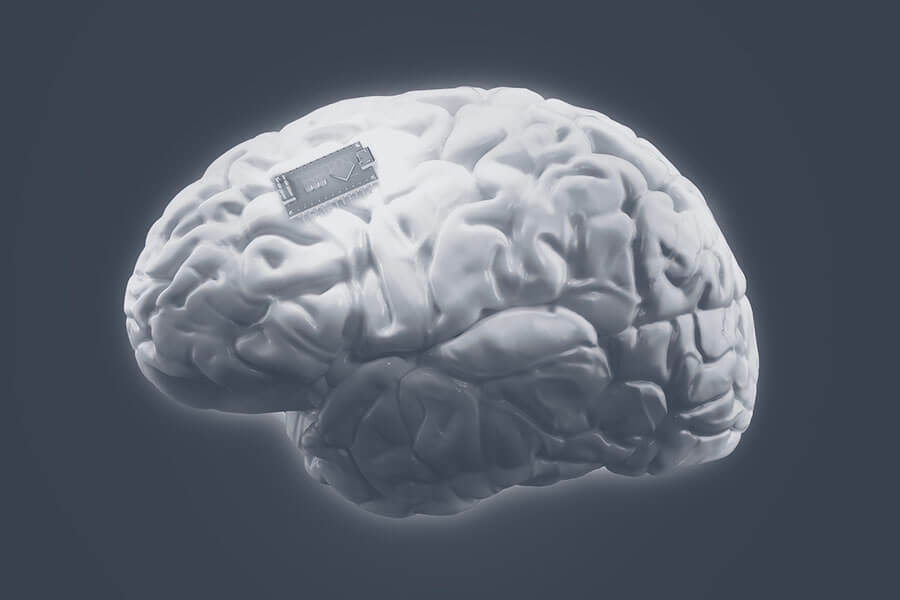
POSITION
2018 bis 2021
Das Ziel des POSITION-Projekts bestand darin, innovative Ansätze für „intelligente“ Katheter und Implantate zu nutzen. Dieses Ziel wurde mit Hilfe von offenen Technologieplattformen für die Miniaturisierung, In-Tip-AD-Konversion, drahtlose Kommunikation, MEMS-Transducertechnologie und Verkapselung verwirklicht. Die verwendeten Plattformen erlauben den Zugriff durch mehrere Nutzer und den Einsatz für unterschiedliche Anwendungszwecke. Die Schwierigkeiten bei der Verkapselung konnten durch Technologien für mehrlagige Beschichtungen gelöst werden, Damit war der Weg frei für die neuste AIMD-Generation langfristig aktiver medizinischer Implantate. Weitere Informationen zu POSITION.
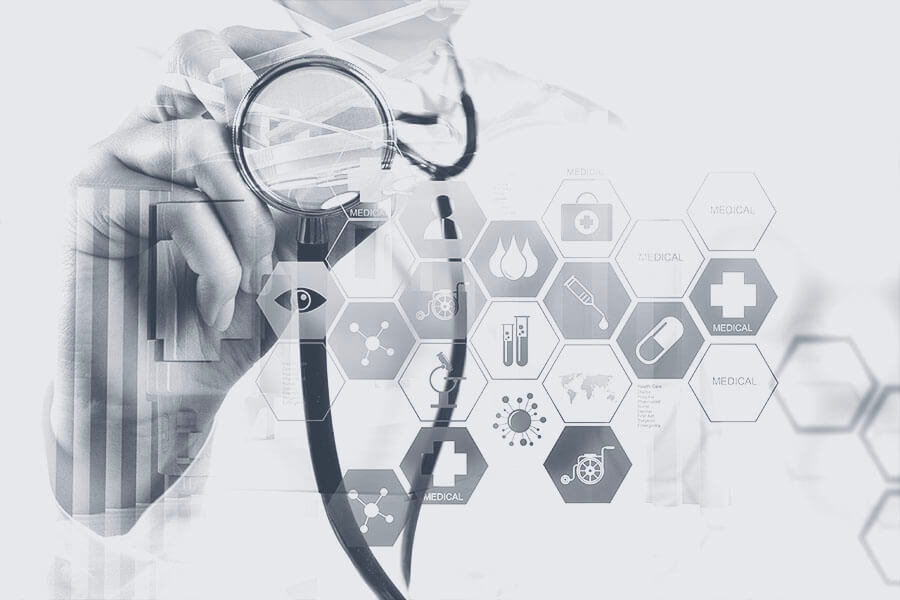
XInoCaps
2017 – 2020
In Zusammenarbeit mit der EPFL entwickelte XInoCaps aus Parylene und anorganischen Materialien mehrlagige Beschichtungen mit effektiven Barriereeigenschaften. In diesen Beschichtungen wurde Parylene C mit dünnen anorganischen (in einem ALD und/oder PECVD-Prozess hergestellten) Folien kombiniert. Dank dieses Projekts konnten die hybriden Geräteplattformen für mehrlagige Beschichtungen verbessert werden. Das EPFL-Labor für die Verarbeitung fortschrittlicher Kompositmaterialien (Laboratory for Processing of Advanced Composites, LPAC) charakterisierte und modellierte dabei die mehrlagigen Beschichtungen, wodurch das mechanische Verhalten und die Schutzleistungen der Barriere verbessert wurden. Das EPFL-Labor für weiche bioelektronische Schnittstellen (Laboratory for Soft BioElectronic Interface, LSBI) integrierte diese innovativen Beschichtungen in elektrisch aktive Geräte und bewertete ihre Leistungsfähigkeit im Hinblick auf die Entwicklung flexibler Implantate, während das Plasmazentrum der EPFL (Swiss Plasma Center, SPC) schwerpunktmäßig am Plasmaquellendesign arbeitete.
Das erklärte Ziel war die Definition mehrlagiger Stapel und Verfahren für die Verkapselung beliebiger Vorrichtungen bei niedrigen Temperaturen. Ein weiteres Ziel bestand darin, die Entwicklung neuer miniaturisierter und flexibler biomedizinischer Implantate mit verbesserter Nutzungsdauer und Zuverlässigkeit zu fördern.
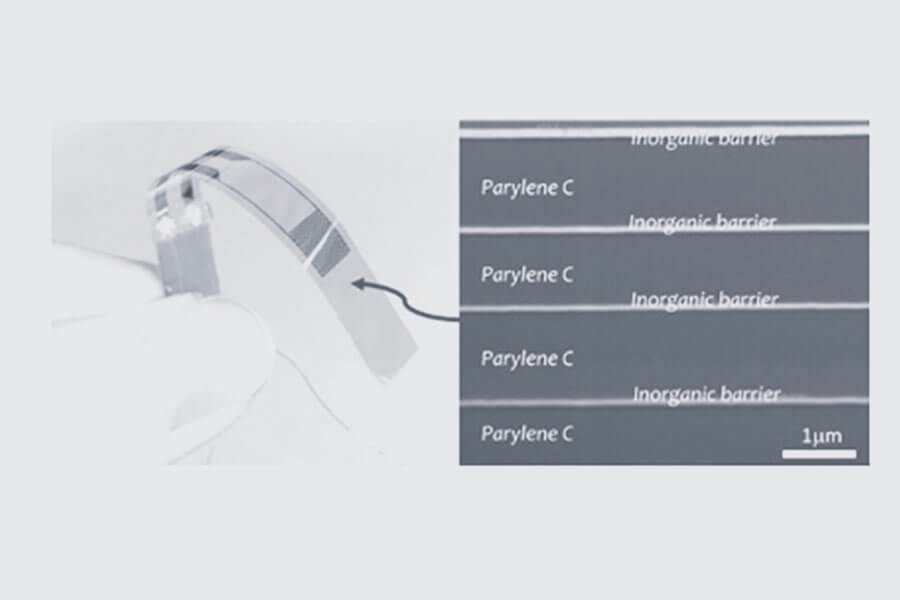
InForMed
2015 bis 2028
Das InForMed-Projekt zielte darauf ab, eine integrierte Pilot-Fertigungsstraße für medizinische Geräte einzurichten. Die Pilot-Fertigungsstraße umfasste Mikrofertigung, Montage und Verkapselung. Im Mittelpunkt dieses Fertigungsprozesses stand die Mikrofertigungs- und Montageanlage von Philips Innovation Services.
Die Verfügbarkeit einer industriellen Anlage für Mikrofertigung und Montage, in der neue Materialien verarbeitet und kombiniert werden können, wies neue Wege für aufstrebende Märkte (insbesondere für die Hersteller intelligenter, minimal invasiver Instrumente und Point-of-Care-Diagnosegeräte) und stimulierte zusätzlich die Entwicklung gänzlich neuer Märkte. Die Pilot-Fertigungsstraße wurde in eine wertsteigernde Innovationskette integriert, die vom technologischen Konzept bis zur großvolumigen Fertigung und Systemqualifikation reicht. Speziell entwickelte Verfahrensprotokolle sorgten für einen effektiven Technologietransfer zwischen den verschiedenen Gliedern dieser Wertschöpfungskette. Die Parylene-Technologie war ein integraler Teil dieser Pilot-Fertigungsstraße und lieferte eine biokompatible Verkapselungslösung.
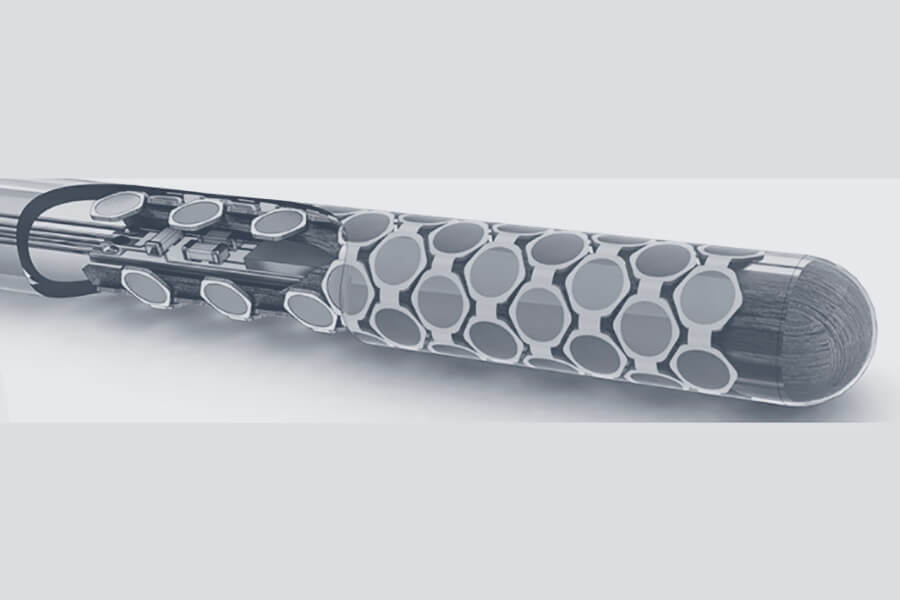